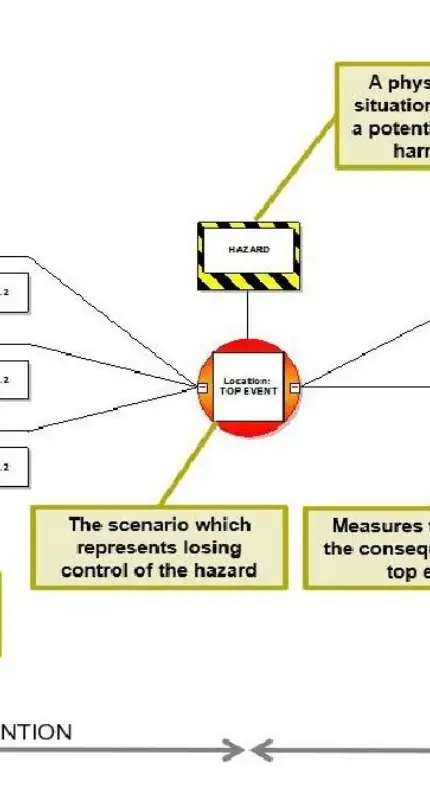
What is BowTie Analysis
BowTie analysis is a risk assessment and management method used to visually represent and analyse potential hazards and their corresponding controls in complex systems.
The methodology is formed by the relationship between Hazards, Top Events, Threats and Consequences and is designed to provide a more functional overview to visualise credible paths from threats to high-consequence scenarios. It provides a clear and concise visual representation of the risks and potential consequences associated with process facilities, making it easier to understand and communicate the risk landscape.
The BowTie diagram itself is shaped like a bowtie, with the top event in the middle and lines branching out on either side to represent threats and consequences. The barriers or controls are shown as lines connecting the causes to the top event. Escalation factors are typically depicted as lines that cross the diagram from one side to the other, indicating the potential weakening of controls.
Commonly used in industries such as aviation, oil and gas, healthcare, and others where understanding and managing risks is crucial to maintaining safety and preventing accidents, BowTie analysis promotes safety, regulatory compliance, and continuous improvement while enhancing communication and decision-making related to risk.
How is a BowTie Analysis conducted?
Defining the scope and objective is always the first step to conducting a BowTie Analysis. A team of multidisciplinary experts with diverse knowledge and expertise relevant to the hazard or risk scenario will begin the process of identifying the central hazard or event they want to analyse (Top Event). Various events or conditions that could trigger the hazards such as human errors, equipment failures, or environmental conditions will be quickly identified (Threats) along with the impact or outcome of these events occurring (Consequences).
The team will evaluate the effectiveness of the current barriers and control measures that are in place and determine if improvements are to be made to prevent the top event from occurring or to mitigate its consequences. These can include safety procedures, equipment safeguards, emergency response plans, etc.
How Gexcon can assist
Gexcon’s team of dedicated process safety consultants can support clients from a wide range of industries with the identification of potential hazards and implementation of risk reduction measures to ensure you maintain regulatory compliance and keep your business running smoothly.