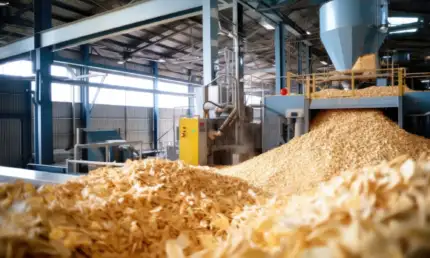
Assess areas requiring electrostatic hazard control
The Electrical Resistance of Dust Deposits (ERDD) test is crucial for evaluating the potential for cone discharges in hoppers and silos especially after processes where the entering dust may have acquired electrostatic charges.
These discharges are a result of the accumulation of electrostatic charges on the surfaces of the dust particles. When the electrostatic potential reaches a critical level, it can lead to a sudden release of energy in the form of a cone-shaped discharge.
The test establishes a specific resistance (resistivity) threshold, setting it at values above 10^10 Ω·m. This limit indicates that dust with resistivity exceeding this level is more prone to cone discharges, emphasising the importance of managing electrostatic risks in hoppers and silos.
Method
This test involves measuring the electrical resistance or resistivity of dust deposits on surfaces.
We perform this test according to EN ISO/EIC 80079-20-2:2016 “Explosive atmospheres – Part 20-2: Material Characteristics – Combustible dust test methods“.
Using a current-to-voltage converter, the electrical resistance of a dust layer's voltage output is measured from which the resistance is calculated using ohm-meters (Ω·m)
The test informs electrostatic discharge potential in hoppers and silos to guide enhancements in product handling and safety measures.
FAQs
-
1Why is the ERDD test particularly important in industrial settings?
In industrial environments, especially those handling combustible dust, the ERDD test is crucial for evaluating the risk of electrostatic discharges, such as cone charges, which could lead to ignition and pose fire or explosion hazards.
-
2What does the resistivity value obtained from the ERDD test indicate?
The resistivity value obtained from the ERDD test reflects the electrical resistance of the dust deposits. A higher resistivity value may indicate a lower risk of electrostatic discharges, while a lower value could suggest an increased risk
-
3How can the ERDD test results contribute to safety measures in industrial facilities?
The test results provide valuable information for implementing preventive measures to mitigate electrostatic hazards. This may include optimising dust control, grounding systems, and other safety protocols in areas prone to dust accumulation.
-
4In which industries is the ERDD test commonly applied?
The test is commonly applied in industries handling combustible materials, such as chemical processing, food production, and metalworking.