Advise on all aspects of process safety during the final phase of development and installation of a new LNG storage facility.
Tasks
- Creation of a 3D geometrical model of the facility to be implemented within FLACS.
- Gas dispersion, jet fire and pool modelling studies to assess a range of scenarios and determine the design and location of additional risk reduction measures.
- A HAZOP of the facility based on the as-built design.
- LOPA and SIL assessment for relevant scenarios identified during the HAZOP.
- Completion of the hazardous area classification and risk assessment in accordance with DSEAR for both the LNG facility and the production factory.
- Completion of the predictive aspects of the COMAH Safety Report, including a quantitative risk assessment conducted using Gexcon/Shell’s software tools FRED and Shepherd.
- Completion of the technical aspects of the COMAH Safety Report, including development of BowTie diagrams.
- Provision of a range of on-site training, including regulatory roles and responsibilities for management, LNG risk management, factory risk management and emergency response. The site also purchased Gexcon UK’s online course ‘DSEAR and ATEX Made Easy’.
Location
Isle of Skye, Scotland
Consultancy
Advise on all aspects of process safety during the final phase of development and installation of a new LNG storage facility. To complete the predictive and technical aspects of the pre-operations safety report for the site as an upper tier establishment under the COMAH regulations.
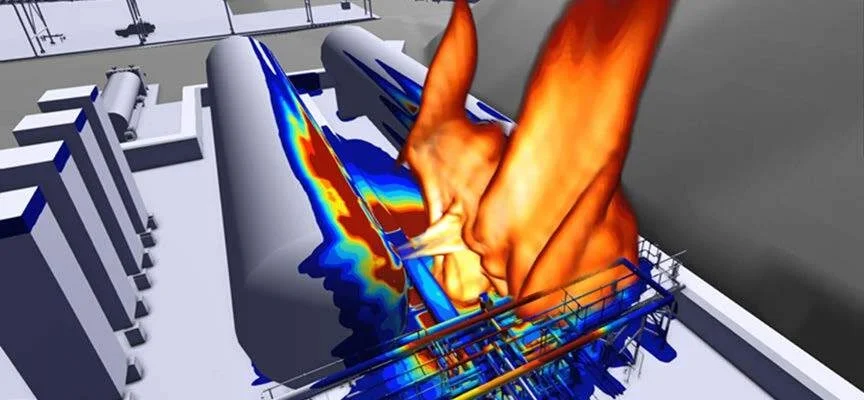
Project Overview
Gexcon were initially contracted to support the production factory with DSEAR compliance. Following issues with the COMAH submission for the LNG facility, Gexcon were then requested to conduct CFD modelling to review the facility design and advise on additional risk reduction measures. The relationship then developed further and Gexcon took the role of managing all aspects of Process Safety, including producing a revised COMAH Safety Report.
In order to conduct the facility design review, the CFD modelling considered a range of release scenarios, including gas dispersion, jet fires and liquid pooling.
The modelling was undertaken in Gexcons propriety software FLACS-CFD. The analysis was used as the basis for key decisions with regards to additional risk reduction measures, including gas detector locations and containment area design.
This provided strong support in both the predictive and technical aspects of the COMAH Safety Report, showing clear justification for the design of mitigation measures. The ability to show a 3D visualisation of potential hazardous events proved invaluable during meetings with the regulator as well as during on-site emergency response training.
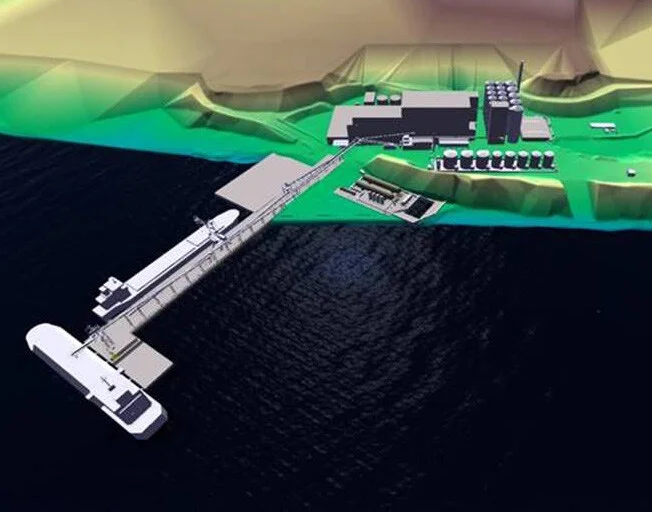
Summary
Gexcon applied a range of process safety services within this project, supporting our client in making significant design changes through to commissioning and operation of the facility.
By applying a thorough and systematic approach, opportunities for additional risk reduction were identified and evaluated during construction, allowing changes to be implemented whilst minimising cost and disruption and most importantly, ensuring the safety of the facility going into operation.
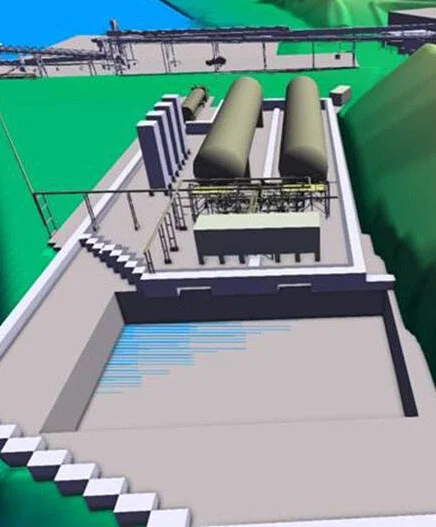