Abstract
On April 17th, 2013, an explosion occurred at the West Fertilizer Company storage and distribution facility in West, Texas. The explosion at West Fertilizer resulted from an intense fire in the seed and storage area of the facility that led to the detonation of approximately 30 tons of ammonium nitrate stored inside a wooden receiving bin. The explosion occurred while emergency services personnel were responding to a fire at the facility. Fifteen people were killed, more than 250 were injured, and numerous buildings were damaged or destroyed.
This paper presents the results of our investigation into the cause and origin of the explosion event, which included:
- early video footage which showed the room where the initial fire originates; and
- applying advanced blast techniques to determine the quantity of ammonium nitrate that likely detonated during the blast.
These techniques included near field blast effects (e.g., the resulting crater left by the blast) as well as the far-field blast damage resulting in the neighboring community.
Introduction
The West Fertilizer Company was owned by Adair Grain Inc. and parts of the property were located in West, Texas. The Seed and Fertilizer building (Figure 1) was built in 1958 and supplied (not produced) fertilizer and seed to farmers up until the date of the incident. In general, the company stored liquid fertilizers (including anhydrous ammonia) in tanks, seed in silos, and solid fertilizer and seed.
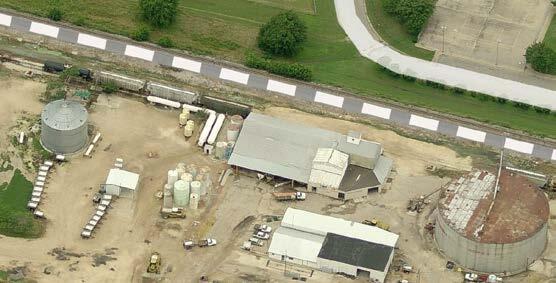
Figure 2 shows the layout of the Seed and Fertilizer building, which included an ammonium nitrate (AN) storage bin neighboring the seed room, as well as an empty bin used for ammonium nitrate storage, and bins containing ammonium nitrate, K-Mag (fertilizer mix of potassium, magnesium and sulfur), Potash, ammonium sulfate, DAP (diammonium phosphate), and a bin for potassium chloride along the west wall.
This building was capable of receiving rail shipments directly from the rail car by means of an underground conveyor belt and bucket elevator; the bucket elevator dumped directly into the northern AN storage bin, or onto a conveyor belt feeding the bins along the west wall. A cross section of the underground conveyor belt and bucket elevator is provided in Figure 2.
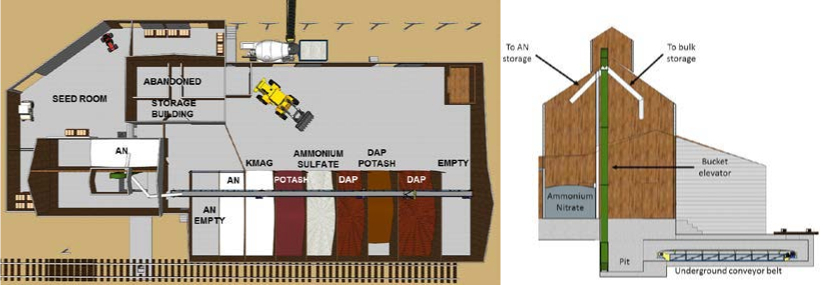
On April 17th, 2013, at approximately 7:29 pm, a fire was reported and fire fighters responded to thefertilizer plant.¹ All operations were already stopped for the day and employees had left the plant at about5:30-6:00 pm. The temperature at the time of the incident was between 78-80°F, and the wind was coming from the SSE at approximately 19 mph. Gexcon obtained several videos that recorded the progression of the initial fire.
Figure 3 shows the initial fire as viewed from the east; note that the highest point on the building represents the location of the bucket elevator by the northern AN storage bin. The image shows that the fire is isolated to the northern section of the building, which includes the seed room and portions of the northern AN storage bin containing about 30 tons of ammonium nitrate.
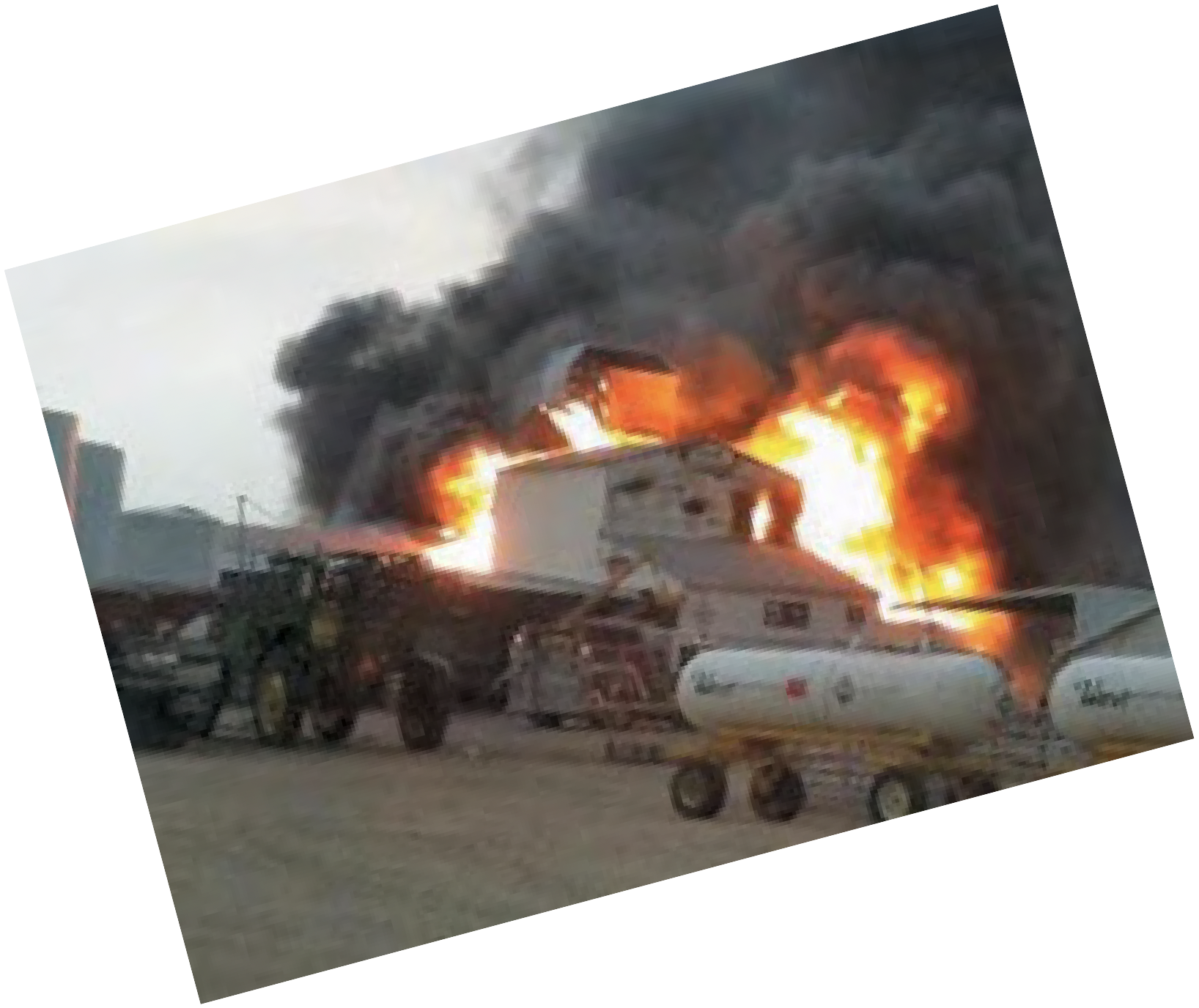
At approximately 7:50 pm, a massive explosion occurred at the fertilizer plant. Figure 4 shows images from a video taken from the high school parking lot to the southeast. Based on the videos from the day of the incident, there were actually two explosions: one smaller blast followed by a larger blast roughly 300 msec later.²
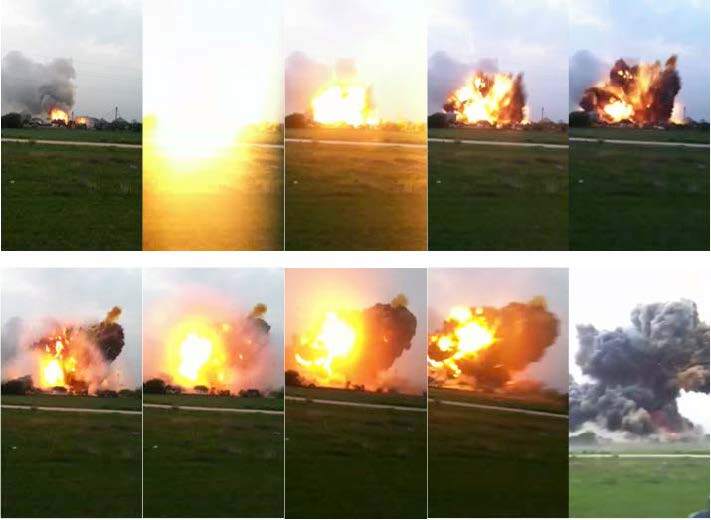
Fifteen people were killed as a result of the explosion, which included voluntary firefighters, and over 250 people were injured.³ Damage was extensive throughout the neighboring community, which included homes, schools, an apartment building and a nursing home.
Investigative evidence
Explosion damage
The blast at the fertilizer plant was massive. It completely destroyed the Seed and Fertilizer and office buildings, as well as the neighboring silos. A rail car with 100 tons of AN was knocked over and the rail road was deformed as the blast propagated towards the neighborhood (see Figure 5). The blast caused a crater approximately 90 feet wide and 10 feet deep1 directly under the northern storage bin containing approximately 30 tons of ammonium nitrate.
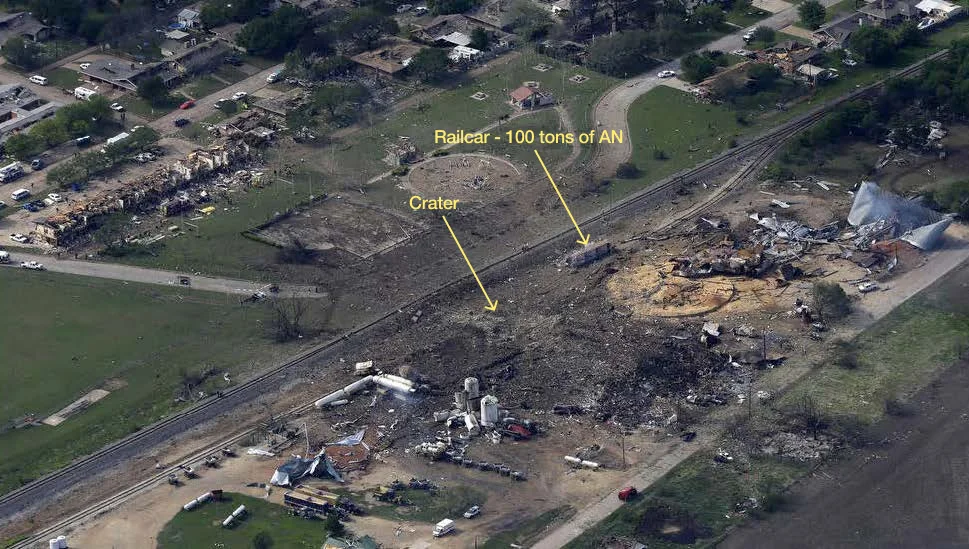
Figure 5. Blast damage as viewed from the southeast
The blast was so powerful that it caused significant damage to the town, which included multiple houses, schools, a nursing home and an apartment complex. Figure 6 shows damage to the apartment complex that was directly west of the facility, just over the train tracks. Windows were broken in houses over a half-mile (~ 1 km) away from the explosion (Figure 7).
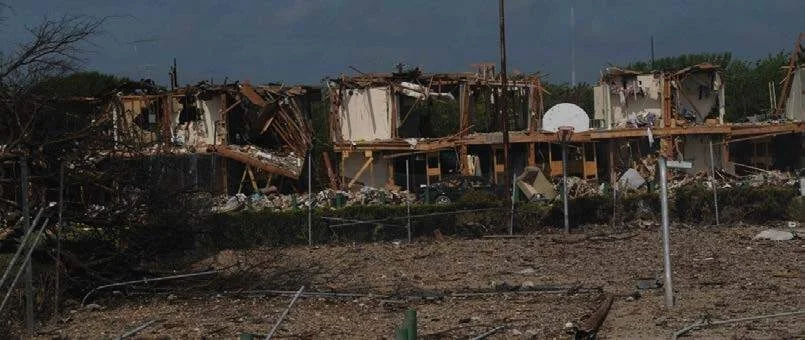
Figure 6. Blast damage to the basketball court and apartment complex west of the plant
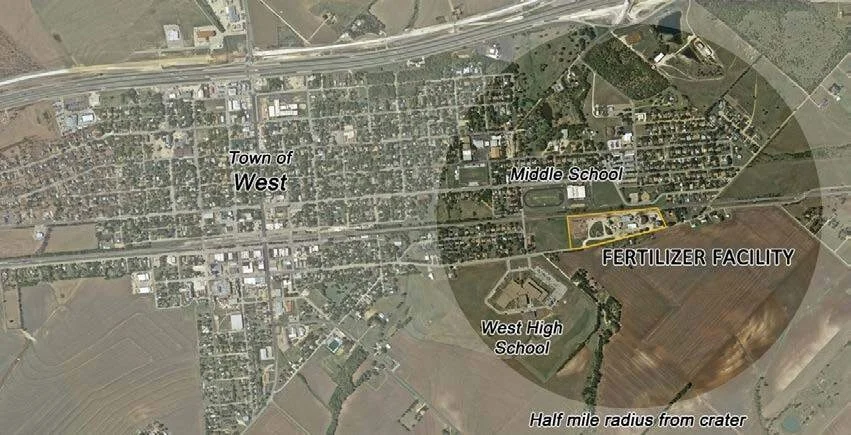
Figure 7. Half-mile radius from the epicenter of the explosion
Ammonium nitrate
Ammonium Nitrate (AN), NH₄NO₃, is a white crystalline or granular solid that readily absorbs moisture. AN is predominantly used in agriculture as a high-nitrogen fertilizer, but it is also an ingredient in the manufacture of blasting agents. AN is not combustible but is a strong oxidizer, which means it can support the combustion of other materials, even in the absence of oxygen. When AN is heated below its melting point it starts to dissociate into ammonia and nitric acid, which is an endothermic process.
Once heated past its melting point, however, the decomposition reactions are all exothermic thus they all contribute to heat generation, further melting the solid AN, and presenting possible runaway conditions.The total energy liberated as the decomposition reactions proceed is known as the heat of explosion. This energy release may ultimately result in a temperature rise of approximately 1,800 to 2,000 °C (3,272 to 3,632 °F) in the immediate vicinity of the explosion.⁴ Since the products of these reactions are all gases, this rapid energy results in a near instantaneous expansion of the gases. These rapid volume increases will typically produce a shock wave that can result in considerable area damage.
The conditions necessary for detonation are not precisely known and have a large variation. However, data suggests that detonations are promoted by severe shock or by heating with confinement. The literature supports the theory that uncontaminated fertilizer grade AN may only detonate under a unique set circumstances that include a severe shock, heating and/or confinement.⁴
Heating AN to its melting temperature (169.6 °C / 337.3 °F) is a major risk because the decomposition gases create a pressure build-up that needs to be vented. AN in the molten state is also sensitive to explosive decomposition.⁵ Molten AN was shown to explode if a significantly powerful force was applied.⁶ In addition, pools of molten AN may form in the event of fire, and if the molten mass becomes confined (e.g., in drains, pipes, plant or machinery) it could explode; this hazard is exacerbated if the AN is contaminated.⁷
Blast modelling
Gexcon performed a blast analysis to determine if the reported quantities of ammonium nitrate present in the northern AN bin could cause the observed blast damage at the scene. When estimating the blast effects of explosives, many blast correlations were developed based on the mass of TNT. Therefore, the “equivalent” mass of TNT that would offer similar blast effects as that for a given mass of ammonium nitrate (AN) was estimated. The TNT equivalency is typically given in %TNT (by weight). While there have been many explosion tests involving AN, the reported values for %TNT equivalent varies over a broad range from 0.42 to 1.0.⁸ ⁹ ¹⁰ Gexcon conservatively chose the lower end value of the range (0.42), which results in smaller amounts of TNT in the blast modeling. It is estimated that at least 30 tons of AN were in the larger AN storage bin adjacent to the Seed Room, so this analysis assumes that 30 tons of AN detonated, which is equivalent 12.6 tons of TNT (11,430 kg).
FLACS-Blast
FLACS-Blast is a module of FLACS that simulates the propagation of blast waves from detonation ofhigh explosives.¹¹ The code does not model the actual detonation process, but solves the Euler equations with a conservative shock-capturing scheme, the so-called flux-corrected transport (FCT) scheme.¹² The FLACS-Blast solver uses the SOLA-ICE algorithm with 2nd order flux correction, instead of the SIMPLE algorithm used by the standard FLACS solver. FLACS-Blast treats the explosive like a bursting “balloon”, which starts with the initial condition of a sphere of high temperature and pressure gases at zero velocity.¹³ ¹⁴ ¹⁵ The base state is estimated based on heat of reaction and temperature of products of combustion (for TNT detonations), which is then isentropically compressed to pressure of 808 bar (consistent with the TNT blast curve).
The equation of state is the ideal gas law. Standard TNT blast curves have been used to establish the empirical scaling relation for the source volume, which is proportional to the mass of explosive material. FLACS-Blast has been demonstrated to match established data for TNT curves. A recent publication has been presented showing very good agreement between experimental results involving C4 detonations in complex environments and the predictions using FLACS-Blast.¹⁶
FLACS Geometry Model of West Fertilizer and Neighborhood
Using topographical data obtained from aerial flyovers and photographs taken of the site (e.g., Google or Bing), Gexcon constructed a 3D model of the plant and surrounding neighborhood. The model included the plant, almost the entire town of West Texas and neighboring areas (Figure 8).
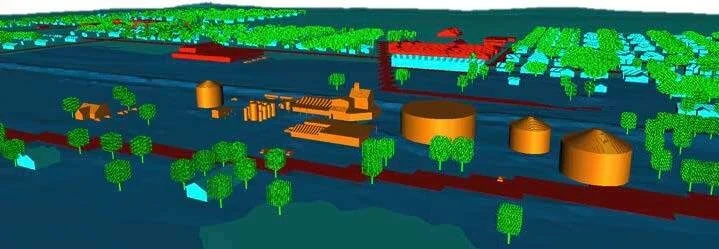
Figure 8. View of the model of the fertilizer plant as viewed from the east
FLACS simulations
By using FLACS-Blast, Gexcon has evaluated the strength of the blast based on a given mass of detonating ammonium nitrate, and compared the results with the observed damage. This analysis focused on the overpressure damage to the apartment complex and various homes in the far field in West, Texas. It was estimated that at least 30 tons of AN were present in the larger bulk storage bin before the explosion, hence Gexcon used 30 tons of AN to estimate the available quantity of AN that detonated. Recall the equivalent mass of TNT is approximately 12.6 tons, which was used as the input to the FLACS-Blast simulations.
Figure 9 shows an example of the resulting blast waves propagating in 3D from the FLACS-Blast simulations of detonating 30 tons of ammonium nitrate. Figure 10 shows a blast wave hitting the apartment complex just west of the facility: the upper overpressure limit is set at 0.29 barg (~4.3 psig shown in red) which results in an approximate side-on pressure approaching 0.15 barg (~2.15 psig). The reported damage effects of blast waves near this magnitude include: “Partial collapse of walls and roofs of houses”, “Lower limit of serious structural damage,” “Concrete or cinder block walls, not reinforced, shattered”, and “50% destruction of brickwork of house”,¹⁷ all consistent with the damage observed to the apartment complex shown in Figure 6.
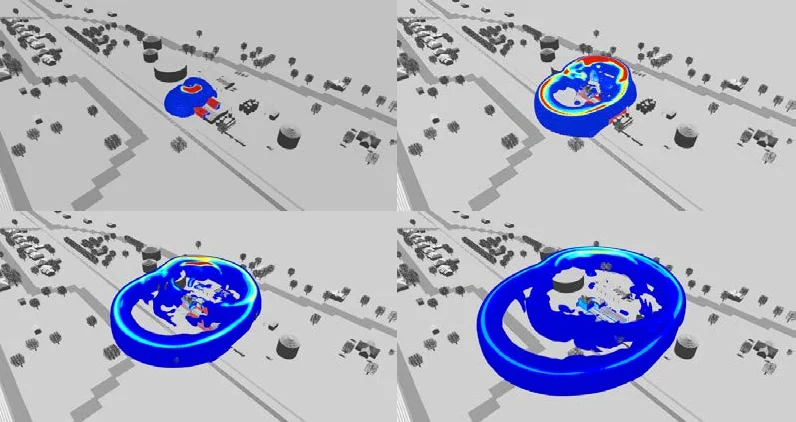
Figure 9. Simulations of a 3D blast wave propagating from 30 tons of detonating ammonium nitrate (red is pressures > 1.0 barg, and blue = 0.01 barg)
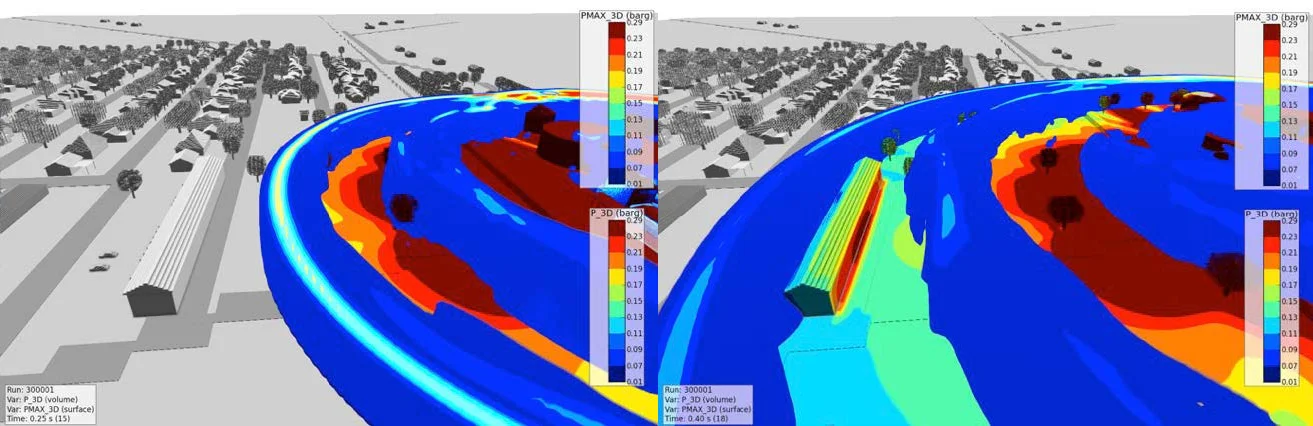
Figure 10. Simulations of a 3D blast wave propagating from 30 tons of detonating ammonium nitrate (red is pressures > 0.29 barg, and blue = 0.01 barg).
Figure 11 shows that the free-field overpressures greater than 0.01 barg extend well beyond identified homes with broken windows. The results of the FLACS analysis are consistent with observed damage in and around the West Fertilizer facility, therefore confirming that 30 tons of uncontaminated AN would be sufficient to generate the far field blast effects that occurred on April 17th, 2013.
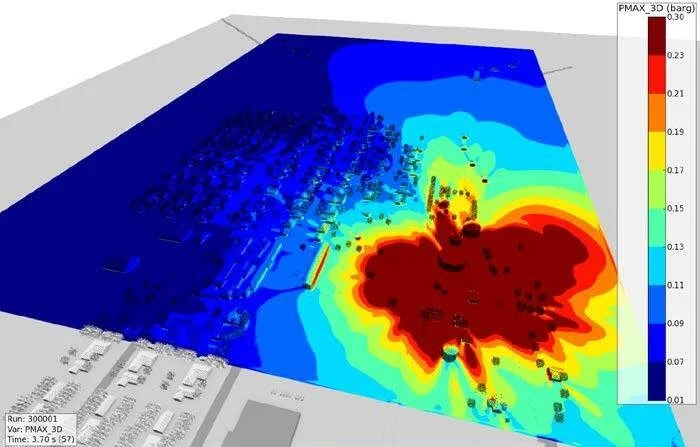
Figure 11. Maximum pressure from blast wave propagated from detonating ammonium nitrate (red is pressures > 0.3 barg, and blue = 0.01 barg).
Crater analysis
The Bureau of Alcohol, Tobacco, Firearms and Explosives (ATF) performed a detailed crater survey utilizing standard surveying equipment to obtain critical crater features, which included but was not limited to apparent crater depth and diameter. The ATF also requested that the U.S. Army Engineer Research and Development Center (ERDC)¹⁸ perform an additional photogrammetric crater survey as well as 3-D scan of the crater and surrounding area using a Riegl model VZ-400 LiDar scanner. The crater was noted to be quite asymmetric. The ATF crater contours from data collected between April 28th and May 8th, 2013 (Figure 12) gives a crater depth of 10.045 feet below the ammonium nitrate bin and 6.676 feet below grade.¹⁹ The crater diameter was reported as 93 feet for this cross section.
While the ERDC reported that the three surveying techniques (standard, photogrammetric, and LiDar) resulted in similar measurements, they reported standing water at the lower portions of the crater that caused the LiDar scans and photogrammetric to show slightly smaller crater depths. As these techniques do not penetrate past the water surface, they will only report depths to the top of the water’s surface and resulted in shallower depths by 0.6-0.7 feet.
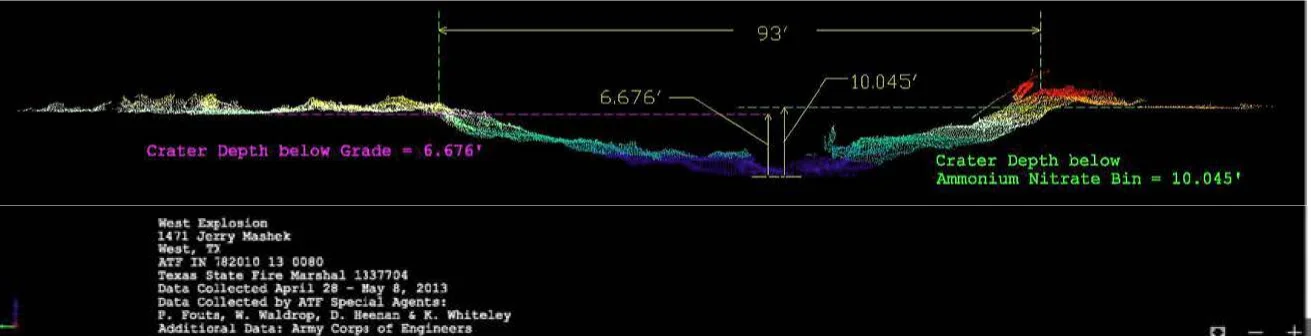
Figure 12. ATF crater cross section.
Figure 13 shows the ERDC Dry Fertilizer Building floor plan and the ATF crater²⁰ overlaid on the Gexcon Dry Fertilizer Building floor plan; the lip of the crater is outlined in red, with the deepest portions in blue. Figure 13 shows the significant asymmetry of the crater and that the deepest portions of the crater were located under a portion of the bucket elevator pit, a section of the northern AN storage bin and one area at the northern side of the same AN storage bin. The placement of the crater is consistent with those recreated at the scene (see Figure 14¹).
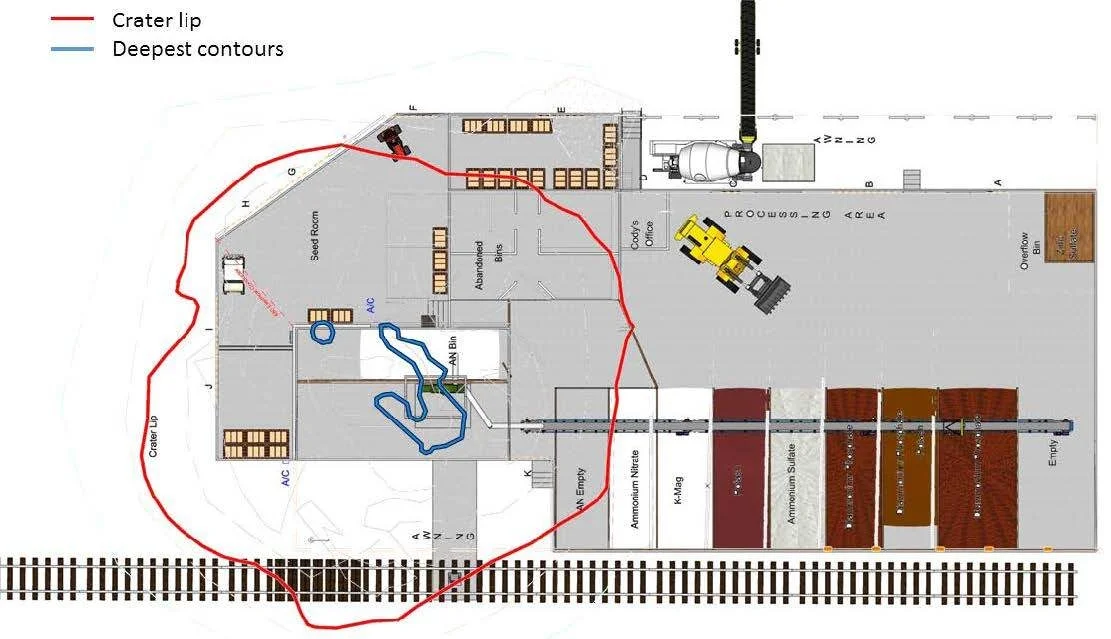
Figure 13. Crater overlaid on a diagram of Dry Fertilizer Building based on ERDC crater survey.
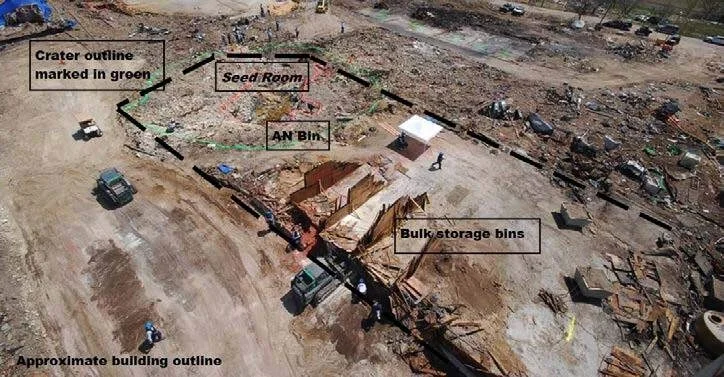
Figure 14. Crater at the West Fertilizer facility.
Gexcon analyzed the ERDC LiDar data coupled with the ATF surveying measurements for the crater using ESRI’s software ArcScene© 10.4.5524. By isolating the crater portion of the dataset and setting the deepest location to 6.676 ft below grade, the volume of earth displaced was calculated to be approximately 11,456 ft³ (324 m³).
ERDC also performed an analysis aimed to define the properties of the materials that cratered during the explosion.¹⁸ A series of samples were obtained from both inside and outside the crater and at different depths. A rapid soil analysis was conducted on the samples and they indicated that the near-surface geology of the crater was somewhat variable, but determined that the near-surface material profile consisted of a concrete slab (8-inches in the sampled area) underlain by approximately 1.5 ft of moist to wet clay that was underlain by rock. The ERDC further reported that, based on soil maps, the soil is classified as a silty clay 10- to 30-inches deep overlying rock.¹⁸ The ERDC further reported that the nearsurface rock in the explosion area is from the Austin Chalk formation, which is primarily comprised of limestone with varying amounts of chalk. The ERDC team noted that small pieces of the slab and rubblized concrete were seen in and around the crater. However, no intact slabs from the pit or northern AN storage bin were found in their original location within crater.
T. J. Flanagan performed a series of experiments to find a correlation between the dimensions of craters created from different TNT charges on the surface of dry-lake playa at Frenchman Flat at the Nevada Test Site in 1966.21 The results of the experiments and the subsequent scaling analysis gave the following first order correlation between the volume of the crater V (m3) and the mass of TNT W (kg):

Using the volume of the crater calculated with the LiDar data and an exponent in the previous formula of 1.111, the mass of TNT is given by:

Based on the AN/TNT equivalence of 0.42 described previously, the mass of Ammonium Nitrate is approximated as:
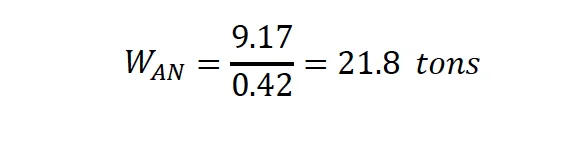
V. V. Adushkin and B. D. Khristoforov also performed experimental studies of craters of chemical surface explosions with commensurable heights of the center of mass and TNT equivalents on soils of different types.22 According to their study, the following empirical dependence of the crater volume as a function of the TNT equivalence in soft soils with shallow and deep bedding of rocks is given by:
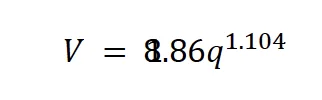
where V is the crater volume in m3 and q is the TNT equivalent in tons (1 ≤ q ≤ 100 tons). Using the calculated crater volume and TNT equivalence, the required mass of AN is given by:

Both correlations are consistent with the quantity of ammonium nitrate reported at the plant and expected to have been stored in the northern AN bin. The correlations also resolve the near field damage observed at the site for the detonation of approximately 30 tons of AN.
Another correlation between the equivalent mass of TNT, the geology of the terrain and the volume of the resultant crater due to various high explosives developed by K. E. Gould and K. Tempo was applied.10 Due to the complexity of the geology at West (concrete, wet clay, limestone), Gexcon analyzed the correlation based on dry soft rock geology, which was used to estimate the average soil conditions present.
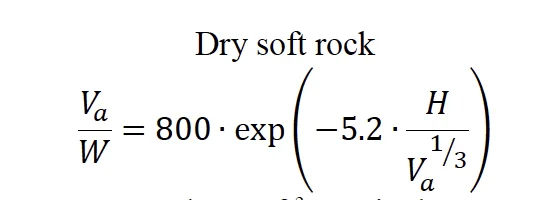
Where Vₐ is the expected apparent crater volume (ft³), W is the TNT-equivalent explosive weight (tons) and H is the height-of-burst (ft).
The results based on the ERDC LiDar data coupled with the ATF surveying measurements for the crater volume of 11,456 ft³, a TNT-equivalent explosive weight of 12.6 tons (corresponding to 30 tons of AN) and a height of burst of 2 ft are shown in Figure 15 as an “x”. The correlation by K. E. Gould and K.
Tempo is consistent with what was observed in the West, Texas incident.
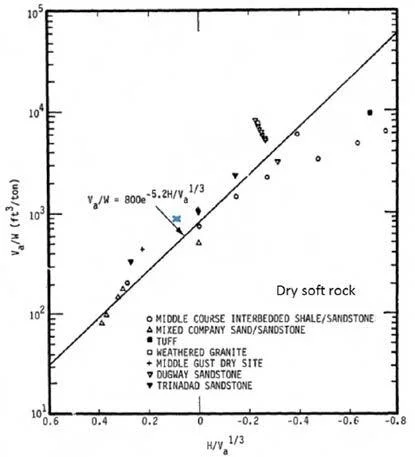
Figure 15. Near-surface HE cratering efficiency in dry soft rock.
Regulations and safety culture
Assistance in the form of code requirements and enforcement for the West Fertilizer facility was limited. In fact, there are no fire or building codes for the County of McLennan or the City of West, Texas.¹ The state of Texas is still one of two states (also Missouri) that lacks a state fire code.²³ Texas even goes so far as to only allow counties with populations exceeding 250,000, or counties adjacent to one meeting the population requirement, to adopt a fire code.¹ NFPA 400 Hazardous Materials Code, which pertains to the storage and handling of ammonium nitrate, contains a retroactivity clause which exempts the West Fertilizer facility (and many other similar facilities) since it was built prior to the issuance of the code.²⁴ The West Fertilizer facility was thus not required to follow National Fire Protection Association (NFPA) or Internal Code Council (ICC) recommendations for the storage of AN.
There are approximately 13,000 facilities similar to West Fertilizer located throughout the United States under numerous jurisdictions.²³ Regardless of the jurisdictional landscape, the existing codes have proven to be limited regarding the safe storage of ammonium nitrate. It is unreasonable to expect an employee of a fertilizer storage facility to have the specialized training and education to understand the complex decomposition of AN, which still lacks agreement in the scientific community, and apply codes and regulations that may or may not be enforced in their region. Nevertheless, West Fertilizer stored ammonium nitrate and handled it safely for over 50 years. As many other facilities in the country have similar practices, it is imperative that the staff of these facilities, and the firefighters committed to protecting these communities, receive training on the hazards associated with ammonium nitrate to prevent a similar event from occurring in the future.
Conclusions
The explosion at West Fertilizer led to fifteen deaths, over 250 injuries, and damage to homes over ó mile away from the facility. The blast resulted in a large crater centered on the northern AN storage bin of the Dry Fertilizer Building. Detailed 3D blast modeling and experimental correlations confirm that 30 tons of AN are capable of causing the observed damage in both the near and far fields. Current codes and regulations are lacking in providing the industry with safe storage and handling procedures for ammonium nitrate. While these codes are improved and adopted, it is imperative that a better understanding of the unique set of circumstances that lead to the detonation of ammonium nitrate is developed and spread throughout the industry. Employees of fertilizer facilities storing AN and the firefighters serving these locations need to be educated on the hazards associated with ammonium nitrate and safe storage practices in order to prevent and manage future incidents.
References
-
1References
¹ Texas State Fire Marshal, "Firefighter Fatality Investigation FFF FY 13-06," West, TX, 2013.
² [Online]. Available: https://www.youtube.com/watch?... and https://www.youtube.com/watch?...OrpKx3aIjA.
³ "A Public Health Report on Injuries Related to the West (Texas) Fertilizer Plant Explosion," June 24,2014.
⁴ J. L. Sherrick, "Fire Risks with Ammonium Nitrate,," Army Ordnance, vol. IV, pp. 237-241, 1924.
⁵ A. W. King, "Threshold Shock Initiation Parameters of Liquid Phase Ammonium Nitrate," vol. International Society of Explosives Engineers, pp. 1-26, 2008.
⁶ R. W. Van Dolah, C. M. Mason, F. J. P. Perzak, J. E. Hay and D. R. Forshey, "Explosion Hazards of Ammonium Nitrate under Fire Exposure," U.S. Department of the Interior, 1966.
⁷ Health and Safety Executive (UK), "Storing and handling ammonium nitrate".
⁸ US Army, "Field manual 5-250: explosives and demolitions," 1992.
⁹ R. Raspet and M. T. Bobak, , "Procedures for estimating the flat-weighted peak level produced by surface and buried charges," US Army Corps of Engineers, 1988.
¹⁰ K. E. Gould and K. Tempo, "High-explosives field tests: explosion phenomena and environmental impacts report," Defense Nuclear Agency, 1981.
¹¹ M. Nolde and T. Skjold, "Blast resistant windows – experiments and simulations," in Twenty-first International Symposium on Military Aspects of Blast and Shock (MABS), Jerusalem, Israel, 2010.
¹² J. P. Boris and D. L. Book, "Flux-corrected transport, I SHASTA – a fluid transport algorithm that works," Journal of Computational Physics, vol. 11, pp. 38-69, 1973.
¹³ H. L. Brode, "Blast wave from a spherical charge," in Physics of Fluids, 2, 1959, pp. 217-229.
¹⁴ D. V. Ritzel and K. Matthews, "An adjustable explosion-source model for CFD blast calculations," in Twentyfirst International Symposium on Shock Waves (ISSW), Great Keppel Island, Australia, 1997.
¹⁵ L. Donahue, D. R. Whitehouse, T. Josey, D. V. Ritzel and P. Winter, "Non-ideal blast effects for vulnerability/lethality analysis," in Eighteenth International Symposium on Military Aspects of Blast and Shock (MABS), Bad Reichenhall, Germany, 2004.
¹⁶ S. Davis and P. Hinze, "Simulating Explosive Pressure in Test Geometries with FLACS-Blast," in Tenth International Symposium on Hazards, Prevention, and Mitigation of Industrial Explosions, Bergen, Norway, 2014.
¹⁷ F. P. Lees, "Chapter 17, Explosions," in Loss Prevention in the Process Industries, 2nd edition, 1996, pp. table 17.43, 17/201.
¹⁸ U.S. Army Engineer Research and Development Center, "West Texas Fertilizer Plant Explosion - Preliminary Site Study and Estimates of Equivalent Explosive Yield," 2013.
¹⁹ Bureau of Alcohol, Tobacco, Firearms and Explosive, "West Crater Cross Section Final 5-11-13.pdf".
20 U.S. Army Engineer Research and Development Center, "West-TX Building-Crater," 2013.
²¹ L. J. Vortman, "Craters from Surface Explosions and Scaling Laws," Journal of Geophysical Research, vol. 73, pp. 4621-4636, 1968.
²² V. V. Adushkin and B. D. Khristoforov, "Craters of large-scale surface explosions," Combustion, Explosions, and Shock Waves, vol. 40, pp. 674-678, 2004.
²³ F. Durso, "Hard Lessons: The West Fertilizer explosion, one year later," NFPA Journal, 2014.
²⁴ "NFPA 400, Section 1.4.1".
About the authors
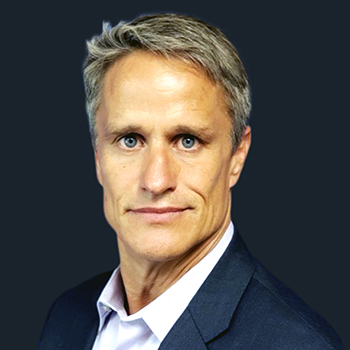
Scott Davis, Ph.D., PE, CFEI
CEO – Principal Engineer @ Gexcon US
Dr. Scott Davis specialises in mechanical and aerospace engineering, and the engineering analysis and testing of combustion, thermal, and fluid processes. Dr. Davis applies his expertise to the investigation, prevention, and risk assessment of fires, explosions, and dispersion hazards such as flammable vapours and toxic exposures. Dr. Davis is a principal member of the NFPA 59A technical committee and provides key training in Gexcon’s advanced safety courses on major hazards, which includes LNG safety. Dr. Davis has published over 100 papers and is a regular speaker at process safety conferences.
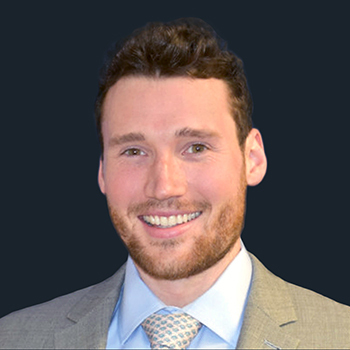
Tom DeBold, P.E., CFEI
Managing Engineer @ Gexcon US
Tom DeBold is an engineer within the Explosion and Fire Safety group at Gexcon US. He specializes in fire protection, mechanical, thermal and fluid engineering. Mr. DeBold performs post-incident investigative work related to fires and explosions. Mr. DeBold has experience in evaluating cause and origin in residential and commercial fires and explosions. He performs incident reconstruction, on/off-site testing, and computational fluid dynamics (CFD) to establish credible accident scenarios. His fire protection engineering expertise includes post-incident fire suppression/extinguishment system failure analyses and review of compliance with applicable codes.
Claudio Marsegan, P.E., CFEI
Consultant @ Blue Engineering and Consulting
Claudio Marsegan is a licensed Professional Engineer (PE) in the State of Maryland who specializes in safety studies for petrochemical plants, with focus on Liquefied Natural Gas (LNG) facilities. Mr. Marsegan uses Computational Fluid Dynamics (CFD) to perform his calculations. He has over 8 years of experience using FLACS and PHAST, focusing on modeling of process facilities, including floating production, storage and offloading vessels, LNG liquefaction and regasification plants, peakshavers and other facilities.
Bryant Hendrickson, P.E., CFEI
Consultant @ Blue Engineering and Consulting
Bryant Hendrickson is a licensed fire protection engineer who specializes in industrial fire protection. He is experienced in performing fire protection evaluations for hydrocarbon processing facilities in accordance with NFPA standards and local codes. Mr. Hendrickson is also skilled in developing and reviewing fire protection design basis documents for fire water systems, fire and gas detection systems, explosion protection, passive thermal protection, and active mitigation systems.