Abstract
On April 26, 2014, at the Georgia Pacific Corrigan plywood facility, a fire that originated at a plywood sander eventually propagated through the pneumatic dust conveying system and resulted in an explosion in the baghouse (dust collector), fatally injuring two employees, and seriously injuring others who were responding to the incident. Sparks from the sander entered the extraction pipe, which was protected by an active suppression/isolation system (spark-sprinkler-abort gate) upstream of the baghouse. When the fire in the extraction pipe was discovered, the extraction blower downstream the baghouse (negative pressure system) was turned off and allowed smoldering and burning to continue within the pipe. The blower was subsequently turned back on, at which time a flame front developed that propagated into the baghouse which was not properly isolated.
This incident occurred because of the improper design of a back-blast damper as an isolation device and operational errors associated with the blower being turned off and back on prior to extinguishing the burning material. More specifically, when designing handling and conveying equipment for combustible dusts, it is crucial to properly implement protective measures (e.g., deflagration venting, suppression, and isolation) capable of mitigating the potential consequences and avoiding escalation of the explosion event when the dust is ignited.
This case study analyses the root cause of the incident as well as key lessons learned related to:
- system design
- performing a dust hazard analysis
- required air stream flow rates
- proper back blast designs
- impeding deflagration vents
- exclusion zones in the path of a vented deflagration in the baghouse
Background
This case study presents an incident that occurred on April 26, 2014 at the Georgia Pacific Corrigan facility, where a fire that originated at a plywood sander eventually propagated through a pneumatic dust conveying system and resulted in an explosion in a baghouse (dust collector), fatally injuring two employees, and seriously injuring others who were responding to the incident. The paper will discuss the proximate causes of the incident as well as key root causes that let to this tragic event.
The Georgia Pacific Corrigan facility manufactured plywood. In the facility, plywood sheets were assembled and cut to size, then sent to the finishing department where the top and bottom surfaces were sanded to the required specification. This was accomplished using a larger belt sander that was automatically fed with plywood sheets.
The finishing sander dust collection system
The belt sander in the finishing department had its own dedicated dust collection system. The system removed wood dust via a pneumatic conveying system that operated under negative pressure. The system comprised conveying pipes, a baghouse, and a blower located downstream of the baghouse. The blower created a vacuum that extracted the dust from the sander through the conveying pipes and into the baghouse.
Vertical pipes extracted dust from multiple locations around the sander (left image in Figure 1). These smaller diameter pipes merged into a larger 36” diameter extraction pipe (referred to herein as the blowpipe), which carried dust across the facility to the baghouse (see right image of Figure 1). Lower than design flow rates were measured in the dust conveying duct work, which often led to material accumulation in the ducts.
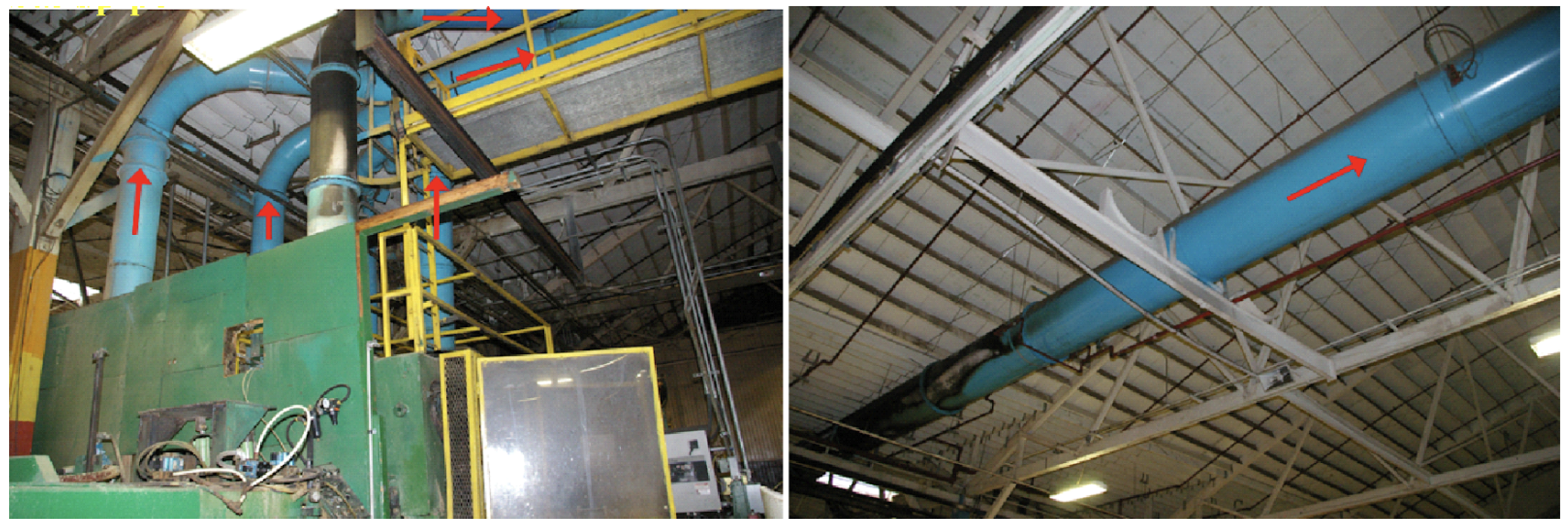
The flow through the baghouse is illustrated in Figure 2. The dust laden airstream entered the baghouse at the base of the cylindrical section. The baghouse then separated the dust from the flow and the clean air exited near the top of the baghouse, passed through the blower, and exhausted out of a vertical stack.
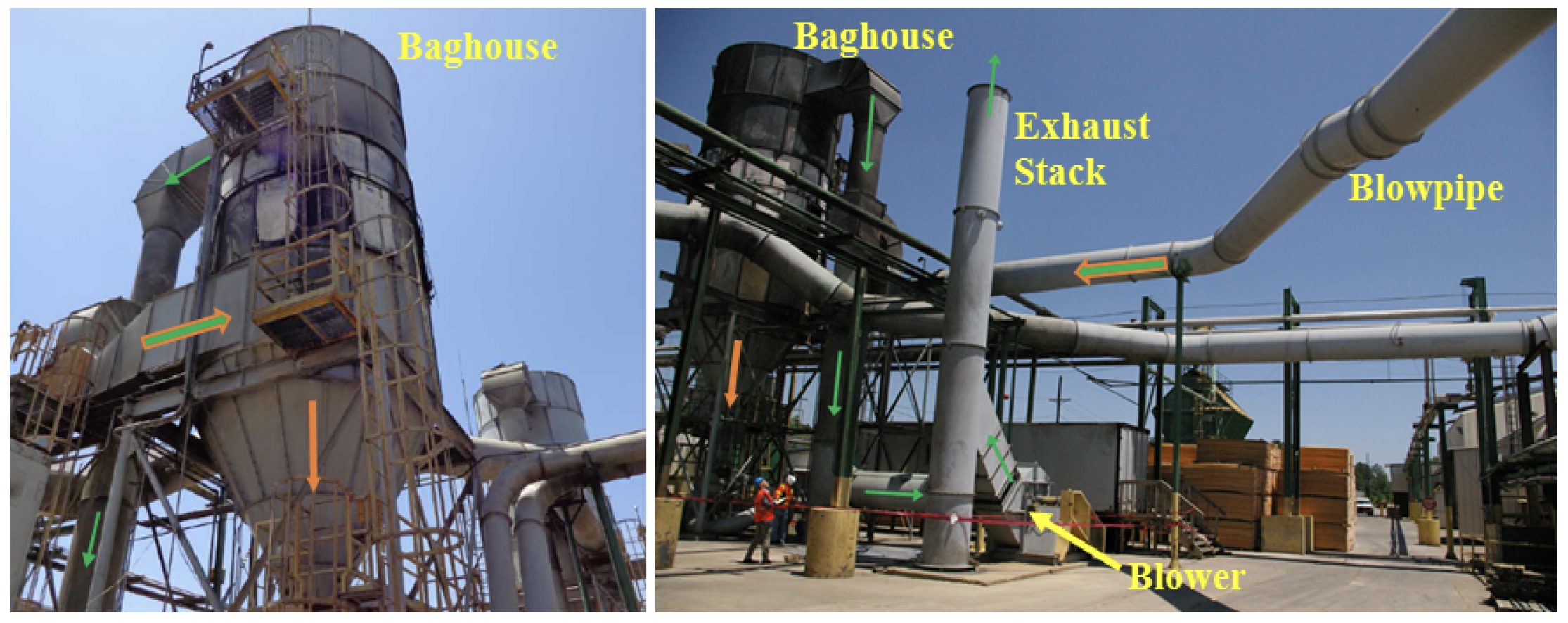
Dust conveying safety systems
Automatically fed belt sanders occasionally produce sparks. Therefore, the dust collection system was equipped with a spark detection system designed to prevent sparks from entering the baghouse. There were two zones intended to detect and suppress sparks using a water mist system and one additional zone intended to detect and redirect sparks using an abort gate if sparks persisted in the flow beyond the suppression zones. Figure 3 shows a two-dimensional diagram of the system. Note that the first spark detection/suppression zone was located in the blowpipe approximately 225 ft from the sander.
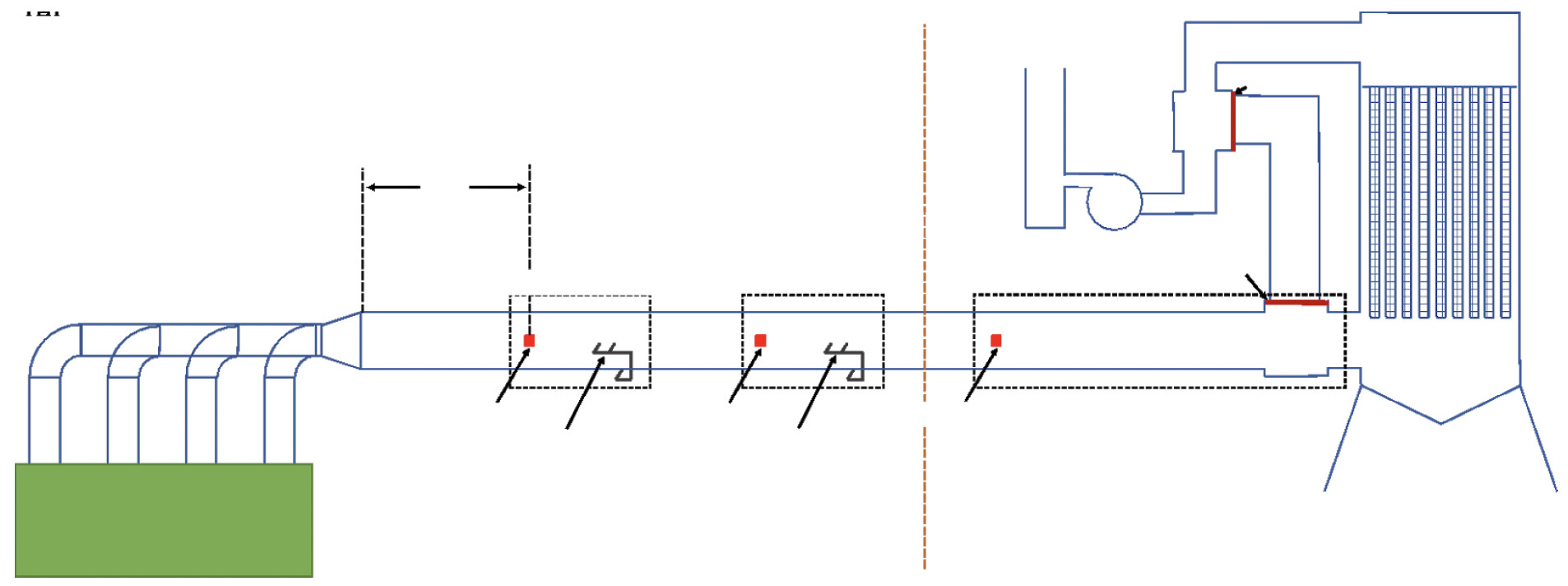
Figure 4 illustrates the flow through the abort gate during normal operation (left images) and the change in flow when a spark is detected beyond the suppression zones (right images) for both the actual configuration and 2D schematic of the system. During normal operation, the gate is positioned horizontally and the flow enters the baghouse. When a spark is detected, the spring-loaded abort gas closes, bypassing flow around the baghouse (see Figure 4).
There was a “back-blast” damper, or explosion isolation damper, installed in the ducting to isolate the clean air outlet of the baghouse from the aborted flow. In general, a back-blast damper is a passive isolation flap valve used on pneumatic systems to prevent flow counter to normal flow. A back-blast damper is designed to keep the valve open when the flow is in the direction normal to the process flow, and when an explosion initiates downstream of the valve and begins to propagate in the opposite direction, the valve closes automatically due to the pressure increase and prevents the flame from propagating past the valve.
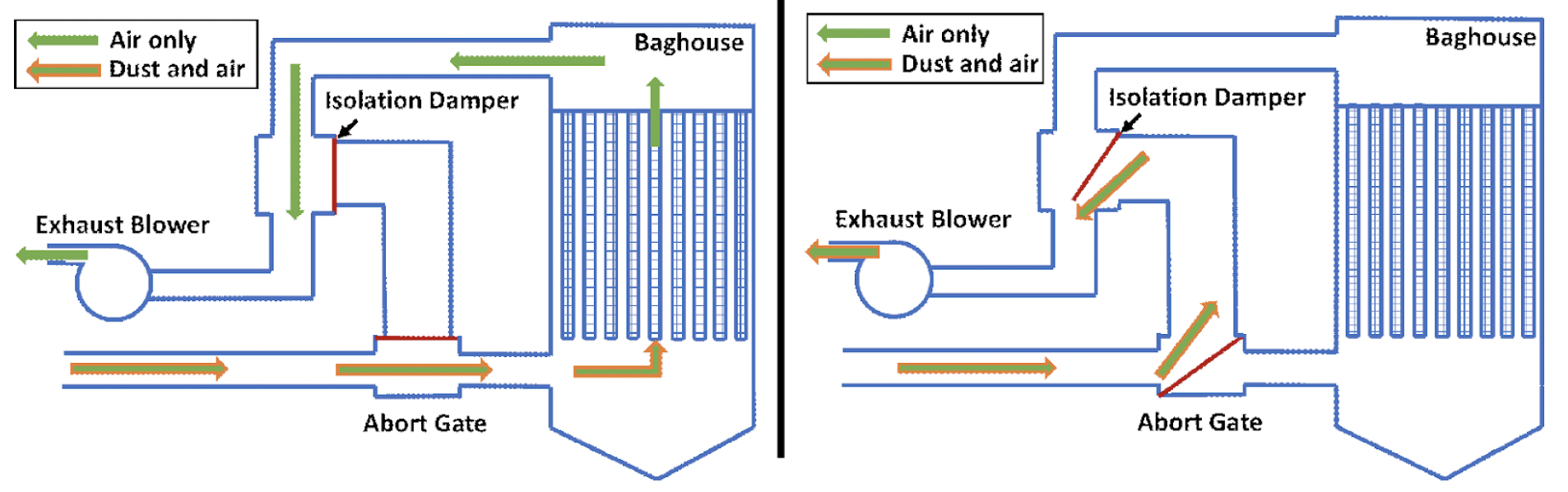
A “back-blast damper”, or isolation damper, was included to prevent potential ignition sources, fire, and/or flame fronts exiting the activated abort gate from entering the baghouse through the clean air outlet. Figure 5 shows where the damper was in the ducting (left image) and provides a close-up image of it (right image).
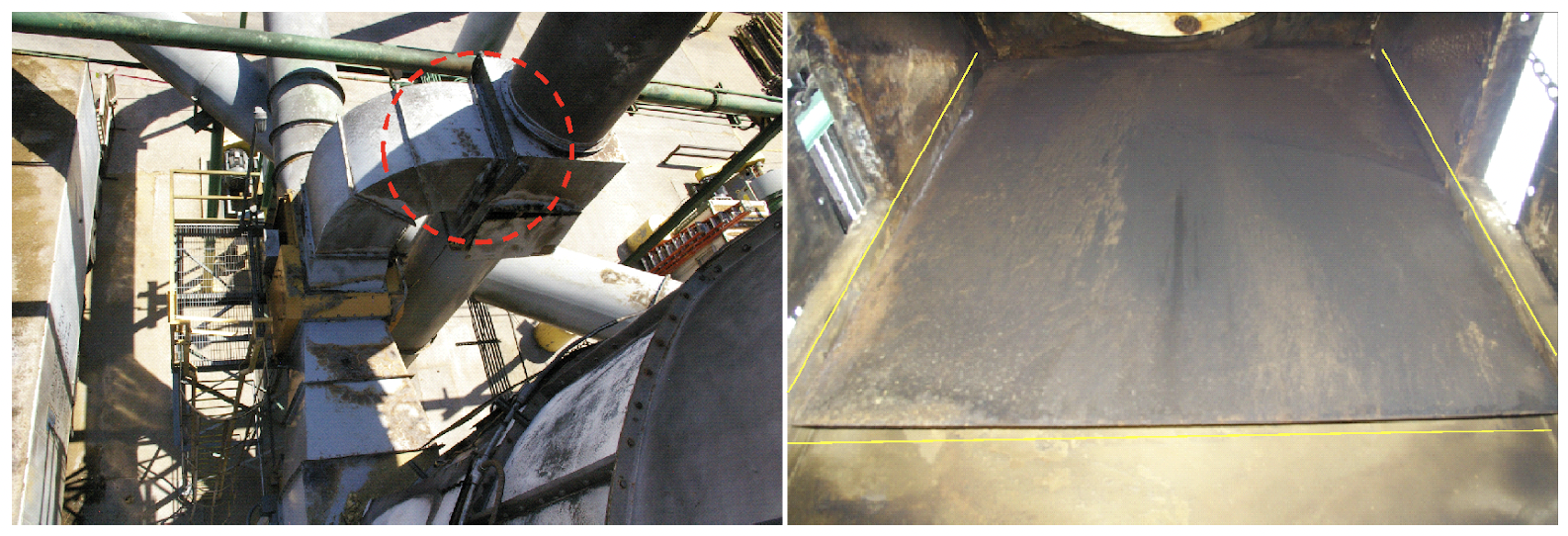
Figure 6 illustrates the intended abort gate and isolation damper positions during normal operation (left image), and when the abort gate is activated and the flow bypasses the baghouse (right image). Arrows in the figure indicate the flow path of both the dust/air streams and clean air. While the intent of the isolation damper was to prevent aborted ignition sources and deflagrations in the conveying system from entering the clean side outlet of the baghouse, when used in a negative pressure system, a damper does not actually create a seal or effectively isolate the baghouse (more details in a following section). Therefore, if a deflagration or fire began in the aborted flow or just upstream the abort gate, it could pass the damper and enter the clean air side of the baghouse (which will be discussed further below), and thus the system had a critical design error.
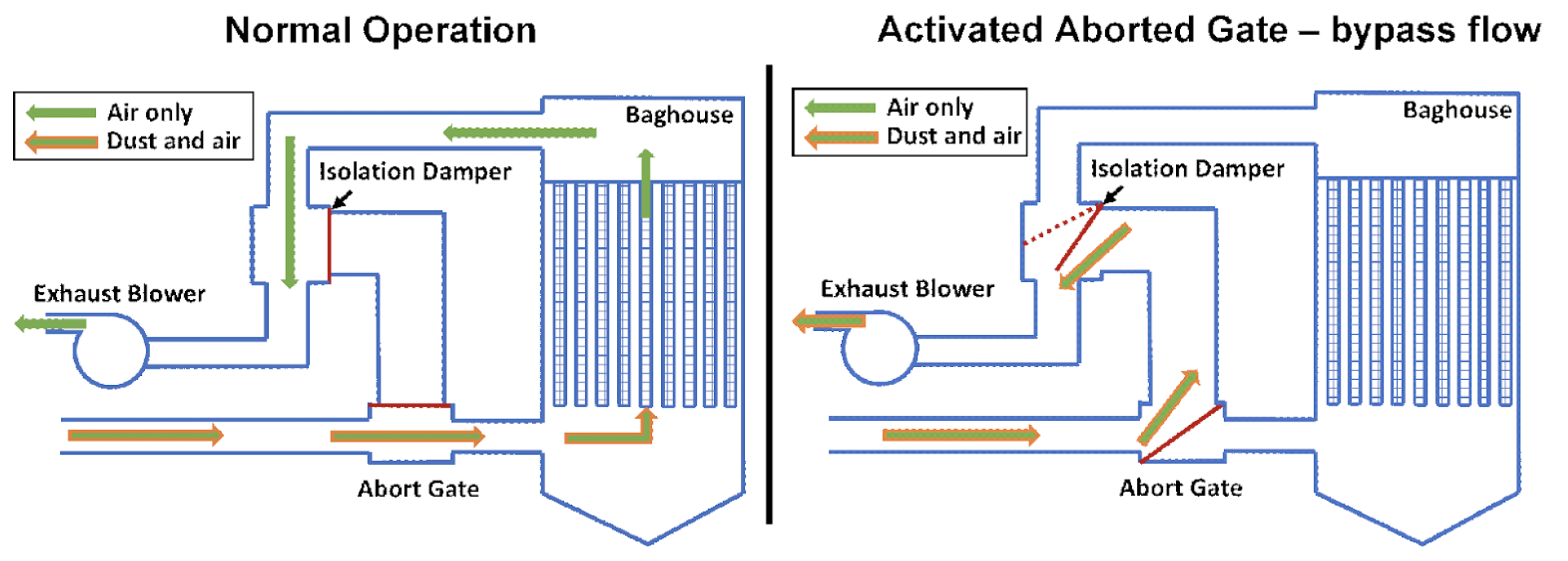
Figure 7 shows the location of the control panel for the blower, which was directly underneath the baghouse.
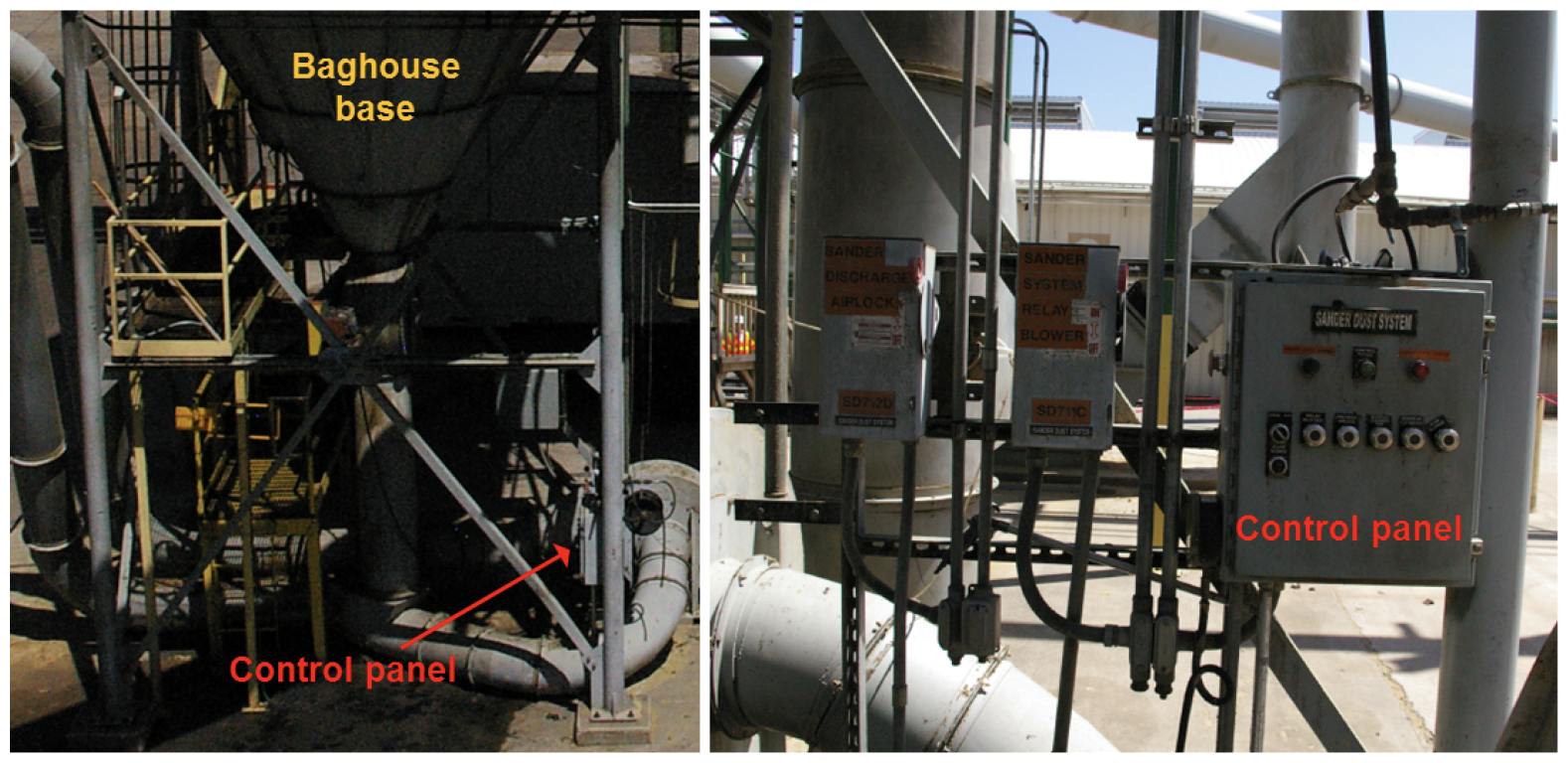
Baghouse deflagration venting
Deflagration vents were installed on the sander baghouse and portions of the ductwork to the baghouse to minimize structural damage in the event of an internal deflagration. The sander baghouse was equipped with 8 vents that were evenly spaced and located at approximately mid-height (see Figure 8). As seen in Figure 8, the vents were also attached to the baghouse with chains so that they would not become projectiles. Vertical filter bags covering steel cartridges were used as the media separator in the baghouse (see right image in Figure 8).
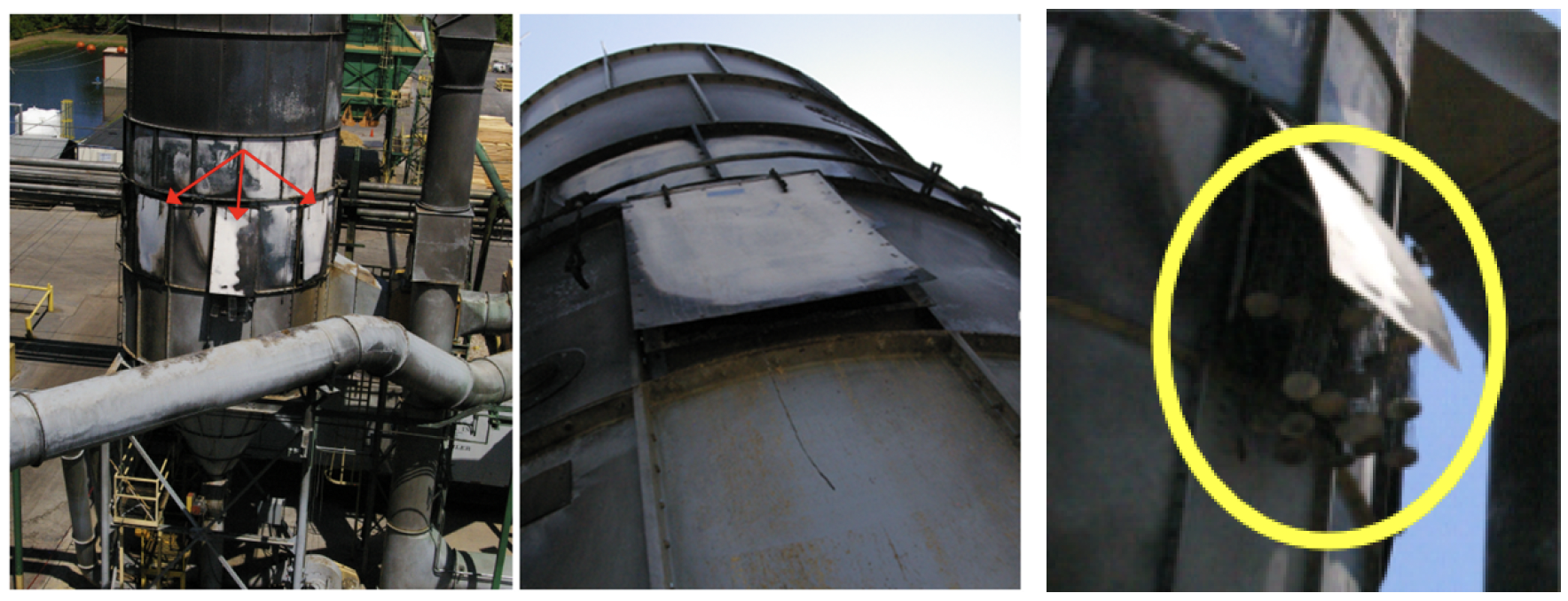
The incident
On April 26, 2014, two plywood sheets were simultaneously pulled into the finishing sander leading to a stoppage. The two employees operating the sander noticed that it had stopped, so they turned off the power and removed the two sheets. One of the operators then opened an access door to the sander and noticed a fire. The operators fought the fire with hand-held extinguishers and eventually extinguished it. All three zones in the ducting detected sparks and reached maximum spark counts (999 count) near the time of the fire. The two sprinkler zones activated and the abort gate opened.
At some point after the initial fire was discovered at the sander, the main blower motor for the dust conveying system was shut off by an employee, resulting in the loss of airflow through the system. Around the same time, employees noticed that a significant portion of the overhead blowpipe was smoking and glowing red, so they began applying water to the blowpipe using a firehose.
Meanwhile, several other employees responded to smoke coming from the blower exhaust stack located near the baghouse. These employees connected firehoses and attempted to spray water into the smoking exhaust stack. Two employees got on an aerial lift to try to gain a better vantage point for spraying water down the stack.
A supervisor then instructed the men to get down from the aerial lift so that he could turn the main blower back on. The controls for the main blower were located under the baghouse. When the supervisor turned the main blower back on, there was a small boom and flames shot out of the exhaust stack. Seconds later, there was a bigger boom, the deflagration vents on the baghouse yielded, and a large fireball propagated out of the baghouse engulfing the immediate area and those within it. The resulting deflagration fatally injured two employees and seriously injured several others responding to the incident.
Cause and origin
Ignition source for the duct fire and explosion
Sparks were generated when two sheets of plywood were pulled into the sander at the same time. The sander is designed to finish boards to a specified thickness, and when the two boards were pulled in together, the greater-than-usual friction between the sander belt and the plywood sheets created sparks.
Cause of the explosion in the baghouse
Sparks were sucked up into the blowpipe when the two boards were simultaneously pulled into the sander. When sparks were sucked up into the blow pipe, stationary dust accumulations in the pipe caught fire. This was evident from: (1) witness statements; (2) the pipe becoming hot enough to ignite the paint on the outside surface; (3) the spark sensors continually outputting a spark count of 999 even though the sander was not in operation; and (4) the burnt accumulations of dust found in certain sections of the blowpipe during post-incident inspections. The abort opened (as confirmed by the as-found position during post-incident inspections) and there was no evidence of a fire in the baghouse (i.e., the baghouse deluge was not initiated). Dust accumulated in the blowpipe because the airstream flowrate through the system was too low due to changes to the equipment during the original installation.
The main blower motor for the system was then turned off by an employee and the airflow through the system stopped. This exacerbated the fire in the blowpipe and allowed it to grow. Due to unclear emergency procedures, the blower was turned back on, and the flow through the blowpipe lifted burning dust nests, embers, and accumulated dust piles and carried them downstream toward the baghouse. These burning accumulations were not extinguished by the spark suppression system as it was designed to: (1) only extinguish sparks; and (2) use a minimum amount of water to not disrupt production every time a spark was detected.
The burning nests and embers initiated a suspended dust cloud deflagration in the dust conveying system which propagated out the exhaust stack and back upstream into the baghouse through the clean air outlet duct (see Figure 9 for illustration). The initial deflagration that entered the baghouse penetrated through the filter bags into the dirty side of the baghouse. It also agitated dust in the bags and created a suspended dust cloud inside the baghouse that ignited and caused a secondary deflagration that was accompanied by the loud boom that yielded the vent panels. When the panels yielded, a large fireball extended downward engulfing the employees that were attempting to control the fire.
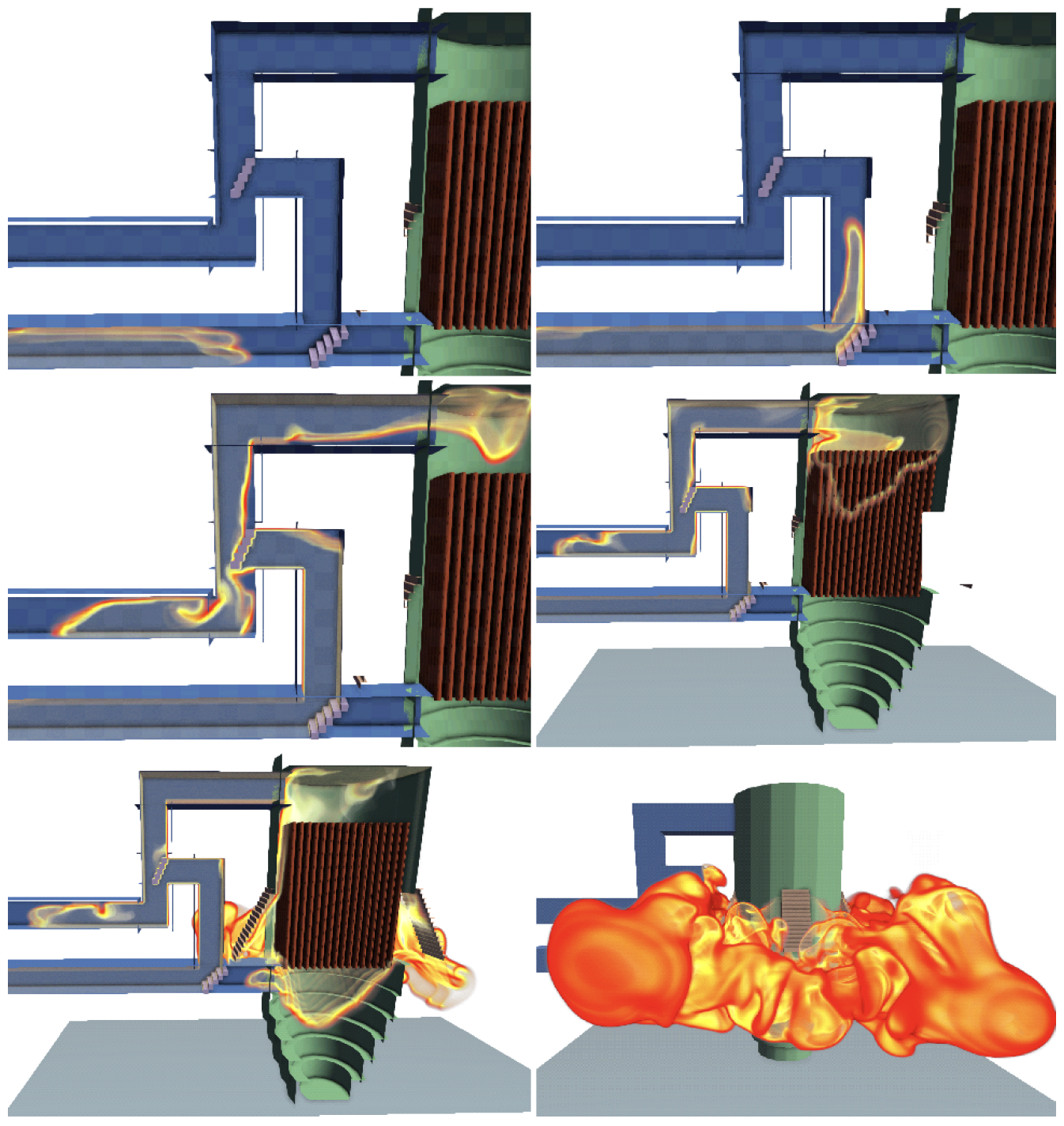
Contributing factors
There were numerous proximate causes of the incident or which led to an escalation of the initiating event. For example, numerous aspects of the dust collection system design were inadequately designed and failed to comply with NFPA Safety Standards, more specifically:
Accumulation of Material
Proper sizing of air-moving devices and ducts to properly capture, control, and convey material and to keep the duct interior clean and free of residual material. Insufficient airstream flowrate in the conveying system allowed dust to accumulate in conveying pipes. A design change to the sheave (i.e., the connection between the electric motor and blower fan) during system start-up resulted in a flow velocity of 3,768 ft/min, well below the original system design of 5,000 ft/min and the minimum recommended velocity of 4,000 ft/min per NFPA 91- Standard for Exhaust Systems for Air Conveying of Vapors, Gases, Mists, and Noncombustible Particulate Solids. Those installing the system and the company never verified the flow velocity through the system after making the change to the sheave.
Lack of Access Ports
Lack of access ports prevented the employees from conducting routine inspections that would have revealed accumulated dust in the conveying pipes. NFPA 91 requires that access doors are provided in horizontal ducts adjacent to elbows, junctions, and vertical ducts
Improper Isolation of the dust collector (baghouse)
As found in the company records, the original design requirements included, “shall supply by-pass duct from the abort valve to the blower unit which isolates the filter unit in case of an emergency”. NFPA 664 - Standard for the Prevention of Fires and Explosions in Wood Processing and Woodworking Facilities2 further requires isolation for conveying systems with fire and deflagration hazards to prevent propagation of fire and deflagration both upstream and downstream into occupied areas or other critical process equipment. As discussed above, the inadequate back-blast damper design allowed sparks/burning dust/flames to enter the baghouse and initiate a dust explosion in the baghouse.
As recommended in NFPA 664, the negative pressure system should have had a second abort gate or equivalent isolation device to prevent deflagrations from traveling back up the clean air outlet duct of the baghouse (see Figure 10). For a negative pressure system, NFPA 664 does not recommend using a single abort gate upstream of the dust collection as this type of system will not clear the ductwork of sparks and embers once the abort gate activates. This is due to leakage through the baghouse that reduces flow in the conveying duct to levels not able to completely purge the sparks and embers from the ductwork.
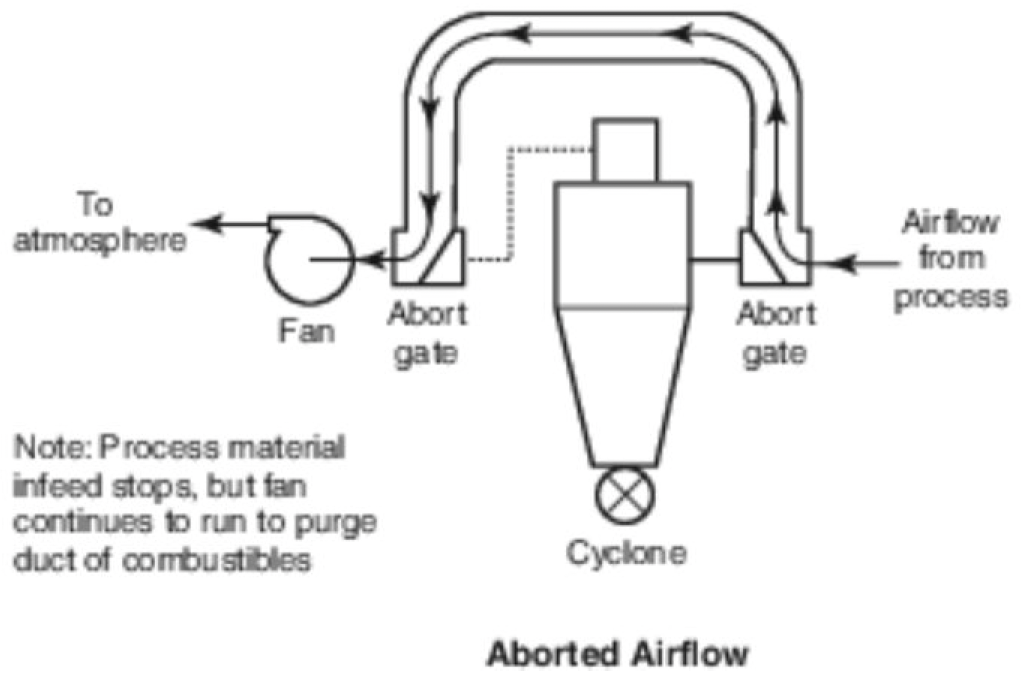
Deflagration venting – exclusion zones
The facility failed to identify exclusion zones in the path of a vented deflagration in the baghouse, and in fact located the system controls underneath the deflagration vents of the baghouse. NFPA 68 - Guide for Venting of Deflagrations requires that facilities consider the size of the fireball that can extend from the dust deflagration vents when choosing the location of vents and vent ducts (see Figure 9). The maximum fireball dimensions also need to be calculated to establish exclusion zones. In addition, appropriate signs need to be provided to warn against deflagration vent location.
Inadequate emergency procedures
The facility owner had contradictory procedures when a fire was observed in the sander, where one procedure indicated to turn off the blower and the other indicated to keep it on. NFPA 652 - Standard on the Fundamentals of Combustible Dust requires the owner/operator to establish clear written procedures for operating its facility and equipment during emergency events. The explosion in the baghouse was initiated by stopping the blower and turning it back on. More specifically, stopping the dust extraction fan to the baghouse and stopping the exhaust of the sparks and fire to the atmosphere, exacerbated the fire condition in the blowpipe. When the exhaust fan was turned back on, air was reintroduced into the blowpipe and lifted burning dusts nests and clouds. The burning material eventually transitioned to a deflagration just upstream or past the abort gate. There were no engineering controls to prevent the blower from being turned off and restarted in the event of a fire in the blowpipe. FM Design Standard 7-73 states that for important pneumatic dust handling systems with multi-zone spark detection, conveying fans or blowers should be left running in all cases.
Deflagration venting – impeded deflagration vent
The cartridges for the bags in the baghouse extended below the base of the deflagration vents. The sander baghouse design drawings indicate that 10’ long bags and cartridges are to be installed. However, measurements made during a post-incident inspection show that 12’ long bags and cartridges were improperly installed. The longer bags reduced the effectiveness of the vent openings and this issue is cautioned against in NFPA 68. This arrangement impeded the venting flow when the deflagration inside the baghouse occurred and could have resulted in a failure of the dust collector with the potential for additional consequences.
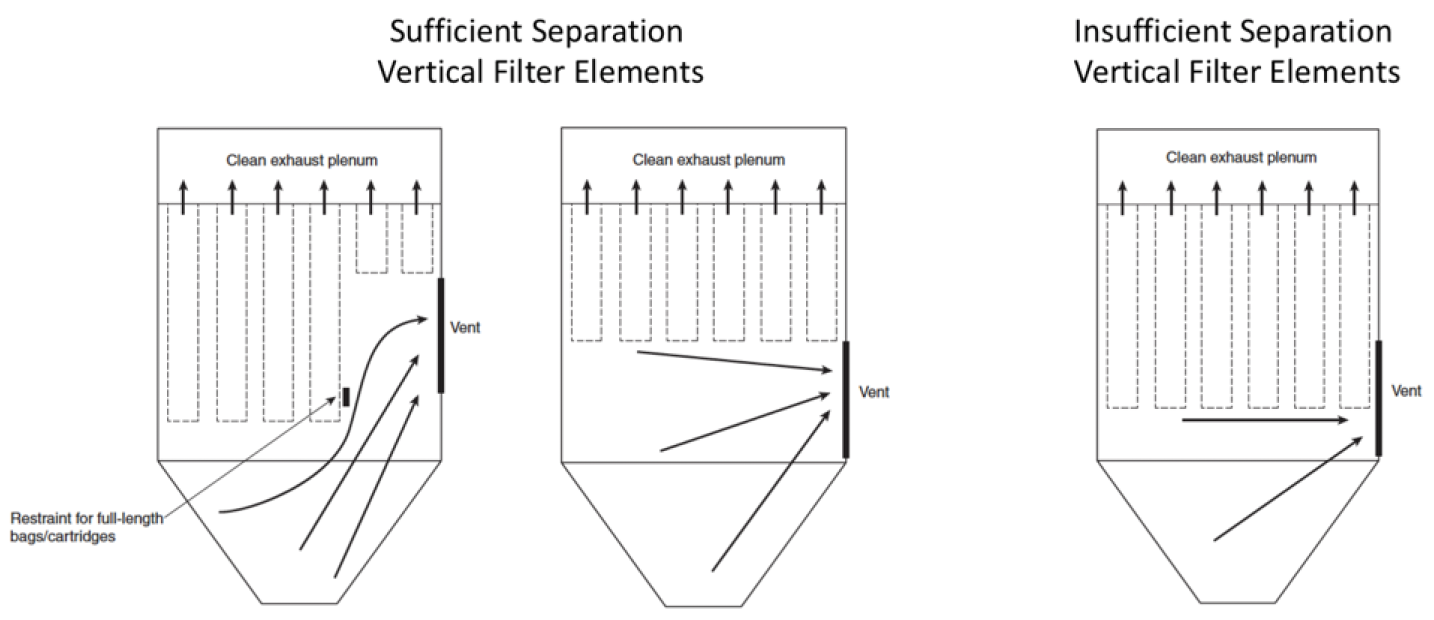
Root cause - Lessons learned
NFPA 654 - Standard for the Prevention of Fire and Dust Explosions from the Manufacturing, Processing, and Handling of Combustible Particulate Solids (2006 and 2012 versions) requires process hazard analyses to be reviewed and updated every five years.
There is no evidence that the owner performed, reviewed or updated the hazard analysis of the dust conveying systems at the plant after they acquired it in 2007. If they had performed a proper process hazard analysis, they could have identified the critical design deficiencies in the sander dust collection system.
More specifically, a thorough hazard analysis and associated evaluation of the existing controls could have identified deficiencies in the system design, such as:
- required air stream flow rates
- proper isolation designs
- exclusion zones in the anticipated path of a vented deflagration
- impeding deflagration vents
Had these hazards been properly identified in a dust hazard analysis, the explosion in the baghouse could have been avoided because:
- Dust accumulation in the blowpipe would have been detected and the low flow rate issue may have been resolved.
- The baghouse would have been isolated from the ductwork. Even if dust still accumulated in the blowpipe and a deflagration occurred inside it, it would not have propagated into the baghouse, resulting in a larger secondary explosion that vented via the deflagration vents.
- Exclusion zones around the deflagration vents would have prevented personnel and controls from being present in the direct path of an ensuing fireball from a vented deflagration.
Conclusion
This incident exemplifies the importance of conducting DHAs in order to not only identify, but prevent or mitigate fires, deflagrations, and explosions from combustible particulate solids.
About the authors
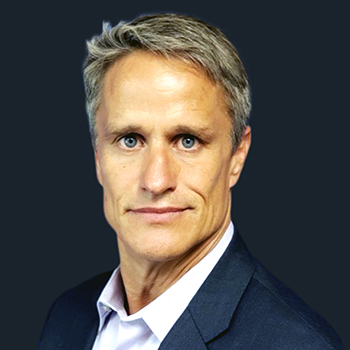
Scott Davis, Ph.D., PE, CFEI
CEO – Principal Engineer @ Gexcon US
Dr. Scott Davis specialises in mechanical and aerospace engineering, and the engineering analysis and testing of combustion, thermal, and fluid processes. Dr. Davis applies his expertise to the investigation, prevention, and risk assessment of fires, explosions, and dispersion hazards such as flammable vapours and toxic exposures. Dr. Davis is a principal member of the NFPA 59A technical committee and provides key training in Gexcon’s advanced safety courses on major hazards, which includes LNG safety. Dr. Davis has published over 100 papers and is a regular speaker at process safety conferences.

John Pagliaro, Ph.D., P.E., CFEI
Senior Managing Engineer @ Gexcon US
Dr. John Pagliaro is a senior engineer at Gexcon US who specializes in the areas of combustion, fire dynamics, heat transfer, thermodynamics, fluid mechanics, and experimental design. He investigates and analyzes fires, explosions, carbon monoxide exposures, chemical releases, and failures involving gas delivery systems, industrial and residential gas-fired appliances, dust handling facilities, heavy machinery, self-reactive materials, and electronic components. Dr. Pagliaro uses numerical and experimental methods to formulate and test cause and origin hypotheses.