A major UK manufacturer began production of hand sanitiser to meet urgent international requirements due to the Covid-19 crisis.
Tasks
An existing plant that traditionally manufactured water-based products containing very minor quantities of flammable materials was being repurposed to manufacture a hand sanitiser that contains a significant proportion of (highly-flammable) alcohol.
This product was to be brought online rapidly, to meet the urgent international requirements due to the 2020 Covid-19 crisis.
An initial assessment identified that without mitigation, mixing tanks would always contain a flammable atmosphere. If this flammable atmosphere was ignited, the explosion would split the tank and propagate the effects of this into the working area, resulting in serious injuries or fatalities.
The conventional way of mitigating this risk would be to blanket the tank with an inert gas, working below the limiting oxygen concentration (LOC). To achieve this, the mixing tank could be sealed, or replaced with one which could be sealed, and an inert gas system would need to be installed along with a process monitoring and control system.
The urgency with which the product needed to be produced precluded this time-intensive approach. We investigated the effects of ventilation on the flammable atmosphere inside the tank under specified manufacturing conditions. The intention was to assess the effect that dilution ventilation would have on the vapour/air concentrations in the tank.
Location
Major UK City
Consultancy
DSEAR Compliance for handling of flammable liquids. Prove the basis of safety needed to produce hand sanitiser that contains a significant proportion of (highly-flammable) alcohol that will show compliance with DSEAR.
Challenges
- Urgent timescales meant traditional methods were unfeasible.
- Alternative approaches needed to be thoroughly proven and shown to be robust.
Software Used
FLACS v10.9 for detailed dispersion modelling
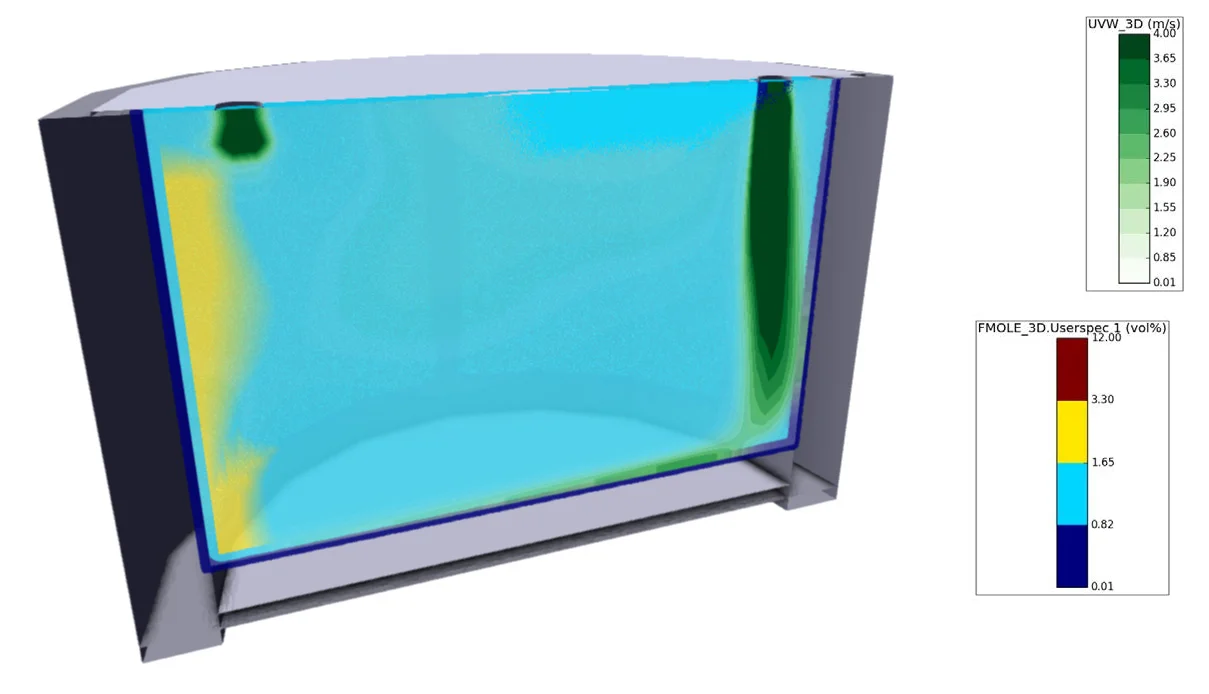
FLACS dispersion modelling results used to determine extraction fan ventilation rates required to avoid the presence of a flammable atmosphere within a stirring tank. The figures show how ethanol vapour concentrations FMOLE_3D (vol%) and the air velocity, UVW_3D (above)/VVEC_3D (next page) evolve over time and demonstrate that vapour concentrations remain below the lower flammability limit (3.3% volume in air for ethanol) for the proposed extraction rate.
Approach
A 3D modelling study was conducted using FLACS-CFD. Different scenarios (such as product loads/levels) were assessed and the impact of varying ventilation rates on the atmosphere within the mixing tank considered. This determined the minimum ventilation rate required to guarantee that a flammable atmosphere could not be formed within the mixing tank.
The ventilation and dispersion modelling study identified that solvent vapour concentration within the mixing tank could be held below the lower explosive limit (LEL)in different scenarios. Increasing the ventilation rate allowed vapours to be below 50% (or even 25%) of the LEL, providing an extra safety gap in the manufacturing conditions.
Benefits
- The detailed 3D CFD modelling of vapour dispersion, provided a clear demonstration that dilution ventilation can be used to guarantee a flammable atmosphere could not be formed within the mixing tanks.
- The modelling permitted the required ventilation rates needed to be determined.
- Using the BowTies study, we demonstrated what additional measures (such as strict operating procedures) would be required to guarantee the safety was robust.
- Quick and pragmatic advice (evidenced by state-of-the-art FLACS modelling), permitted manufacturing to start safely on a timescale to meet the urgent International requirement.
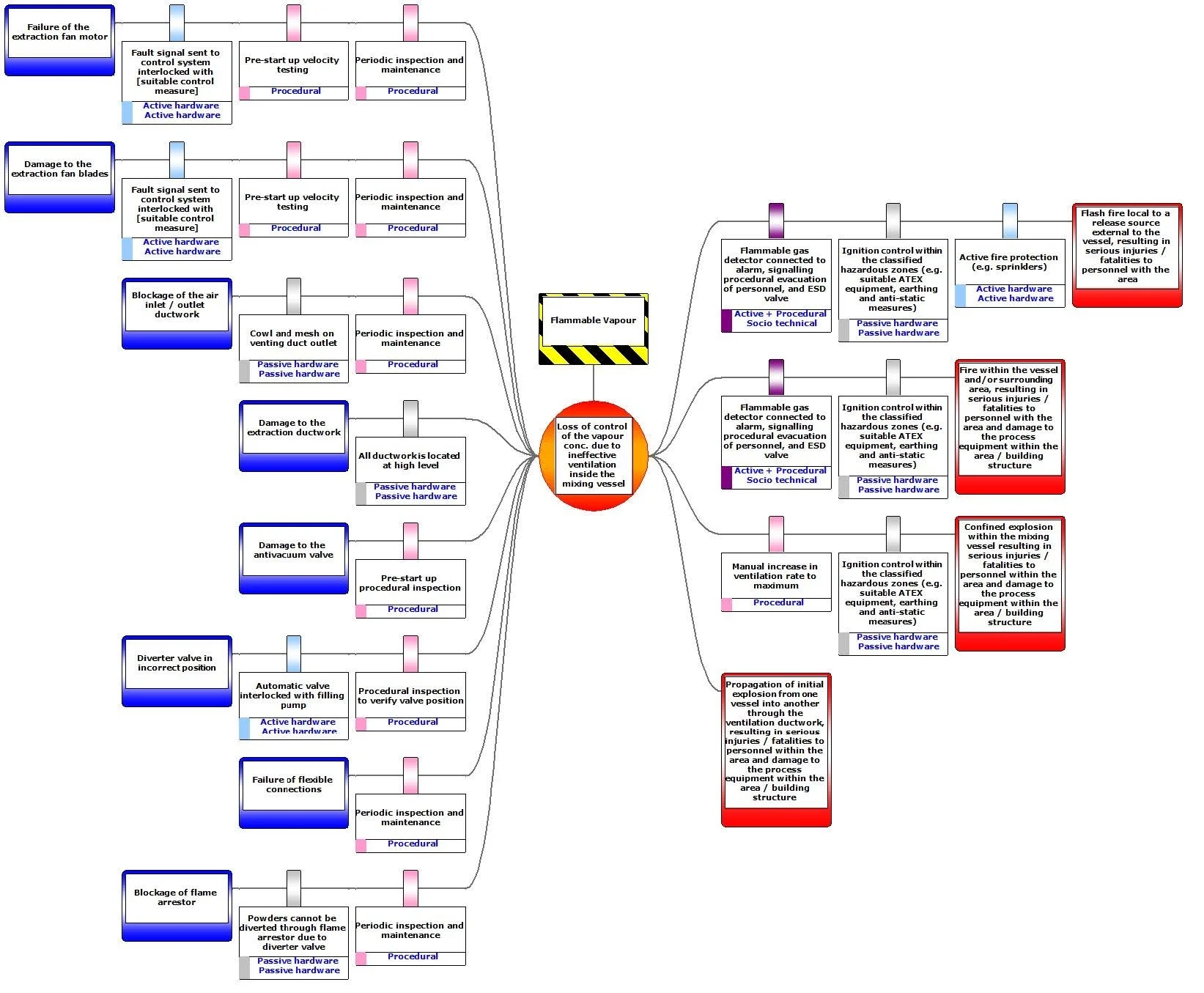
BowTie Diagram showing Vapour Concentration Control Measures
Results
FLACS-CFD modelling confirmed that dilution ventilation could be used as a basis of safety. A BowTie study was used to demonstrate how robust it was, and what additional layers of protection were needed.
The study showed that this approach relies heavily on safe operating procedures and requires intensive operator training. Due to the urgent requirement and the short nature, this was an acceptable approach to ensure safety concerns had been addressed.
Summary
The use of FLACS-CFD, combined with Gexcon’s experience and engineering judgment, permitted the client to clearly demonstrate that the proposed approach of using dilution ventilation combined with training and strict operating procedures would allow the product to be manufactured safely.