A fire accident in a workplace could potentially cause devastating losses. Loss of life, damage to the property, disastrous environmental harm, and financial costs can be severe.
Understanding how to avoid potential fire accidents and how to mitigate the consequences is therefore essential. In terms of mitigation, one of many ways to reduce the consequence of fire is through installing the necessary fire protection.
Fire protection is often divided into Active Fire Protection (AFP) and Passive Fire Protection (PFP).
In this question-answer-based article, we will focus on PFP.
What is Passive Fire Protection?
PFP is a vital construction element installed in a building or on process equipment that prevents or slows down the spread of fire. The purpose can also be to maintain the strength and integrity of process equipment/ process lines.
For example, suppose you have a chemical X that has a self-ignition temperature of Y oC, transported through a steel pipe in your process line. Suddenly, you have a pool fire accident under this pipe. When the pipe reaches 550oC, it begins to lose its strength. If you have covered this pipe with the right PFP, it will take a longer time for the steel pipe to reach the temperature where it starts to lose strength. At the same time, it will also take a longer time for chemical X to reach its self-ignition temperature. During this period, your firefighting team may have enough time to pull out the fire. Hence you can avoid explosions and the devastating losses they may cause.
PFP is called passive because it does not require any action to perform the protection, unlike sprinklers or alarm systems that fall under the AFP category.
However, it is crucial to understand that both PFP and AFP are equally essential and work in coexistence during a fire. AFP functions as a fire detector and fire suppressor. If a fire breaks out, AFP elements such as alarms and sprinklers will be activated immediately after detection. At the same time, PFP will limit its spread.
What are the types of Passive Fire Protection?
There are two types of PFP:
- Resistance to fire: this type of PFP involves its ability to act as a fire-separating element to limit fire spread or prevent the collapse of a load-bearing element.
- Reaction to fire: this type of PFP is related to its surface burning behaviour and its ability to restrict the rapid flame spread and smoke production.
How does PFP work?
PFP works by:
- Limiting the spread of fire and smoke by acting as a barrier to contain them in their area of origin
- Providing sufficient time for evacuations of people from buildings or plants
- Protecting escape routes
- Limiting damage to a building or plant by protecting critical structural components
What are the examples of PFP products?
Examples of PFP products can be as follows:
- Fire doors
- Fire-resistant walls, floors, ceilings and ducts
- Cementitious coatings
- Intumescent coatings
- Fire shutters
- Fire dampers
- Fire-resistant glass
- Spray-applied epoxy intumescent and subliming coatings
- Fiberglass materials
- Penetrations seal systems for pipes, cables, etc.
Why do PFP products need to be tested and certified?
The effectiveness of PFP products depends on their quality. The manufacturers of PFP products need to ensure their products fulfil the required fire-resistant performance. Therefore, PFP products need to be verified through fire testing and certified by a third-party inspector.
PFP testing can be performed in various ways depending on the desired scenario. In our next blog, we will discuss these scenarios.
You can choose testing scenarios based on fire type followed by other factors such as the possibility of corrosion and cryogenic spill.
Need support in testing your PFP products?
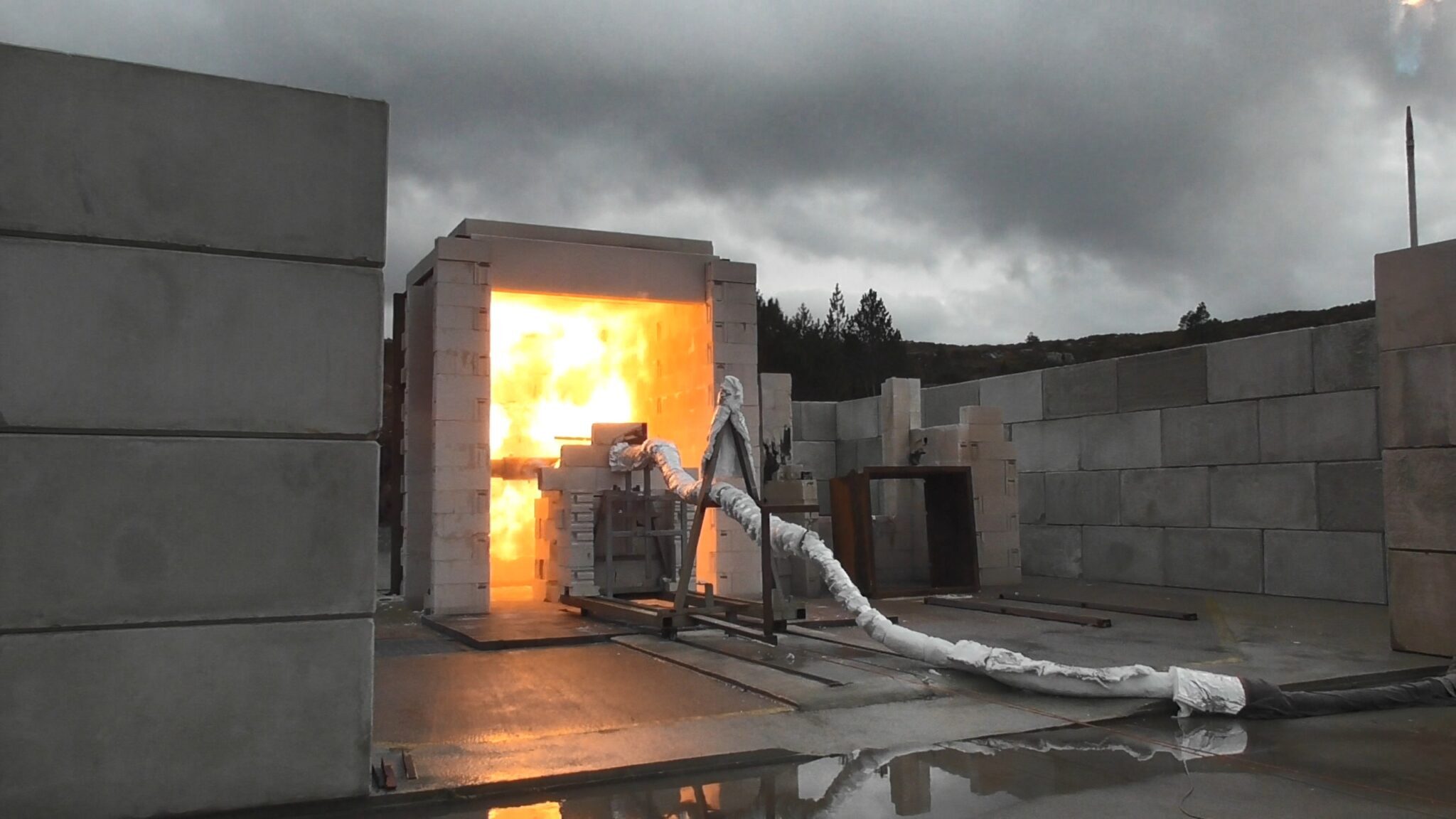
Gexcon’s large-scale jet fire and explosions test centre is located in Sotra just outside the city of Bergen, Norway. We offer various scenarios of jet fire and explosion tests, such as:
- explosion before fire scenario (Blast testing) based on ISO/ DIS 23692-1
- standard jet fire test based on ISO 22899-1
- high heat flux jet fire test (ISO standard for this test is in progress)
- cryogenic spills jet fire test based on ISO 20088-1, -2, and -3
We have tested various materials, including different kinds of spray coating systems, fibreglass and pyrogel systems, PFP jacket systems, penetration seal systems, and many more.