Ammonia has been for many years the refrigerant of choice for businesses with a need for process cooling, temperature-controlled storage and distribution, food and drink manufacturing, and many other applications.
The benefits of using ammonia include high energy efficiency and a reduced global warming potential depending on the fuel mix used to generate electricity.
Even though it is a natural refrigerant there are some challenges to using ammonia which may pose additional risks to a facility and personnel if not stored or handled correctly.
Ammonia hazards
Ammonia is classed as a highly poisonous gas when exposed to high levels, however with its distinctive smell detectable at low levels, and leaks naturally rising and dissipating into the atmosphere due to its lighter-than-air density, these two factors alone could mitigate the hazards of exposure to dangerous levels in occupied areas.
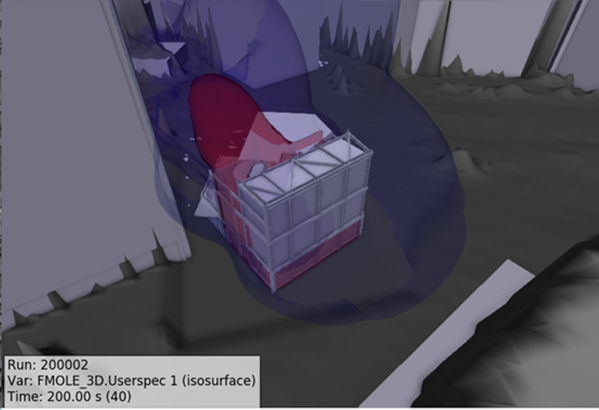
Whilst fires and explosions may not be the greatest hazard relating to ammonia, its occasional classification as a ‘non-flammable’ gas has led emergency responders to the dangerous assumption that there is no risk of igniting a flammable atmosphere. However, Ammonia in the air at concentrations of 15% to 25% volume is flammable and will burn or can explode, particularly if the gas/air mixture is present in a confined space.
When ammonia is mixed with combustible materials such as lubricating oils, its flammability range widens, and because ammonia is commonly stored as a liquid under pressure, boiling liquid expanding vapour explosions (BLEVEs) are theoretically a hazard. For such reasons, precautions against fire and explosions still have to be taken especially for unoccupied parts of the installation.
Risk assessment and safety management
All refrigeration systems require risk assessment and ammonia systems are no exception. The regulatory requirement is different based on the location of the facility and whether it falls under the ATEX Directive or Dangerous Substances and Explosive Atmospheres Regulations 2002 (DSEAR).
The risk of leakage and over-pressurisation of the refrigerator system need to be handled with a strict and robust safety inspection and the appropriate hazardous atmosphere assessments being completed, this includes studies like HAZMAT, HAZOP, SIL and LOPA assessments, which typically include and review operational faults, process control, cause and effects.
The HSE has in the past identified common failures in the understanding of ammonia refrigeration technology applicable to some designers, installers, contractors and site staff. These include, among others, “failure(s) to identify through assessment the likely sources of gas escape so that appropriate plant modifications may be made or appropriate plant checks instituted to detect likely sources of leakage at an early enough stage.”
While locating the plant in a separate building from the main store or workroom is recommended, this may be difficult to implement by building designers. Machinery rooms should be provided with sufficient permanent ventilation during normal operation to mitigate the build-up of toxic concentrations of ammonia from any small operational releases.
Often this can be achieved by mechanical ventilation, inlet louvres or air bricks in external walls fitted at a low level with vents at a high level to facilitate natural circulation, unfortunately on many occasions it has been observed that installers fail to guarantee the minimum required levels of ventilation.
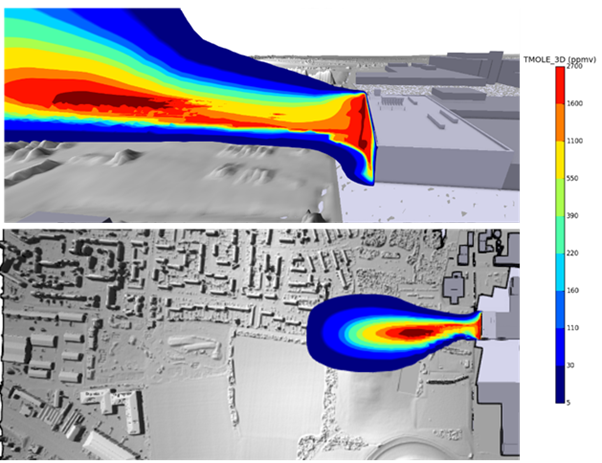
Advanced CFD (computational fluid dynamic) modelling by means of FLACS-CFD can help in improving ventilation/dilution levels in enclosed/open areas and improved detection times from common leaks, as well as gaining insight into the expected dispersion of ammonia upon accidental releases to the atmosphere.